
MSP PerfectPart
Create a 'Perfect Part' with MSP
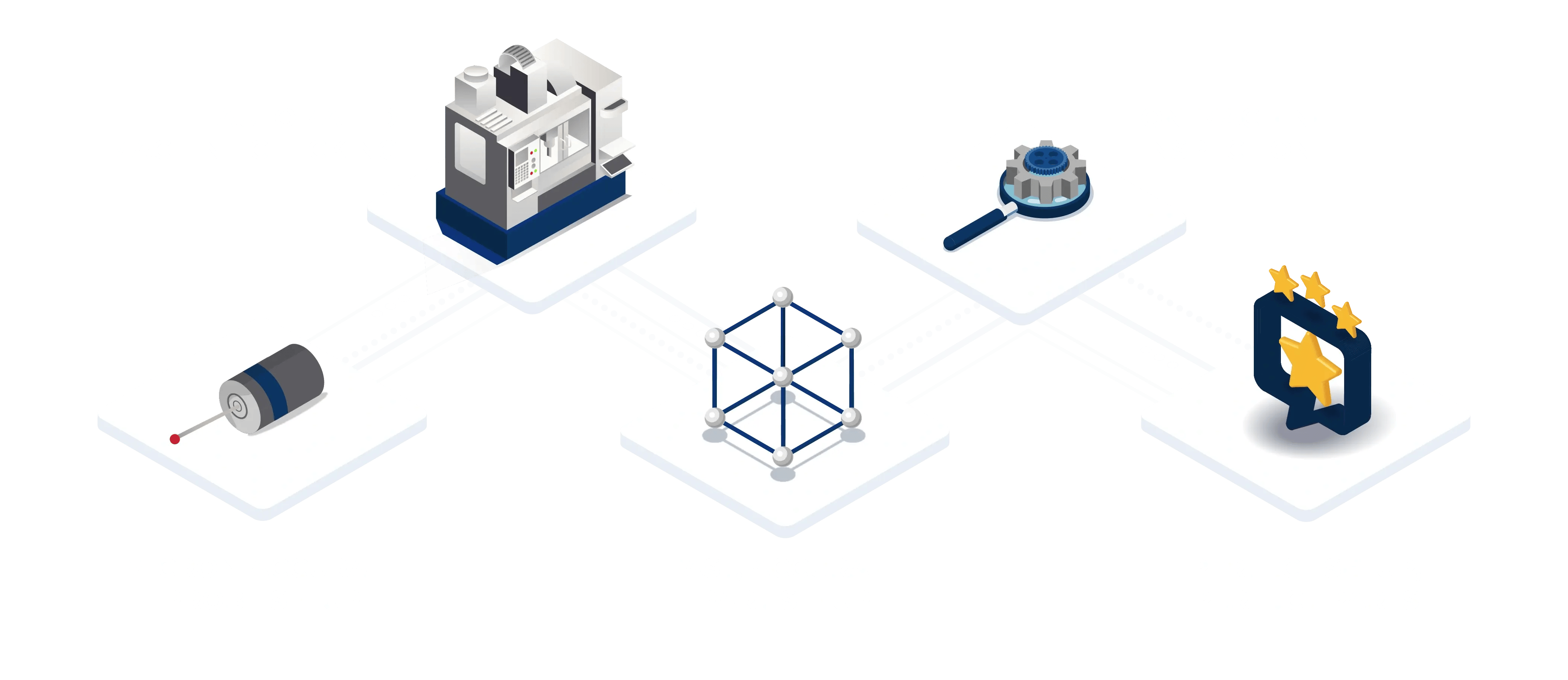
MSP PerfectPart
Make a PerfectPartTM with MSP
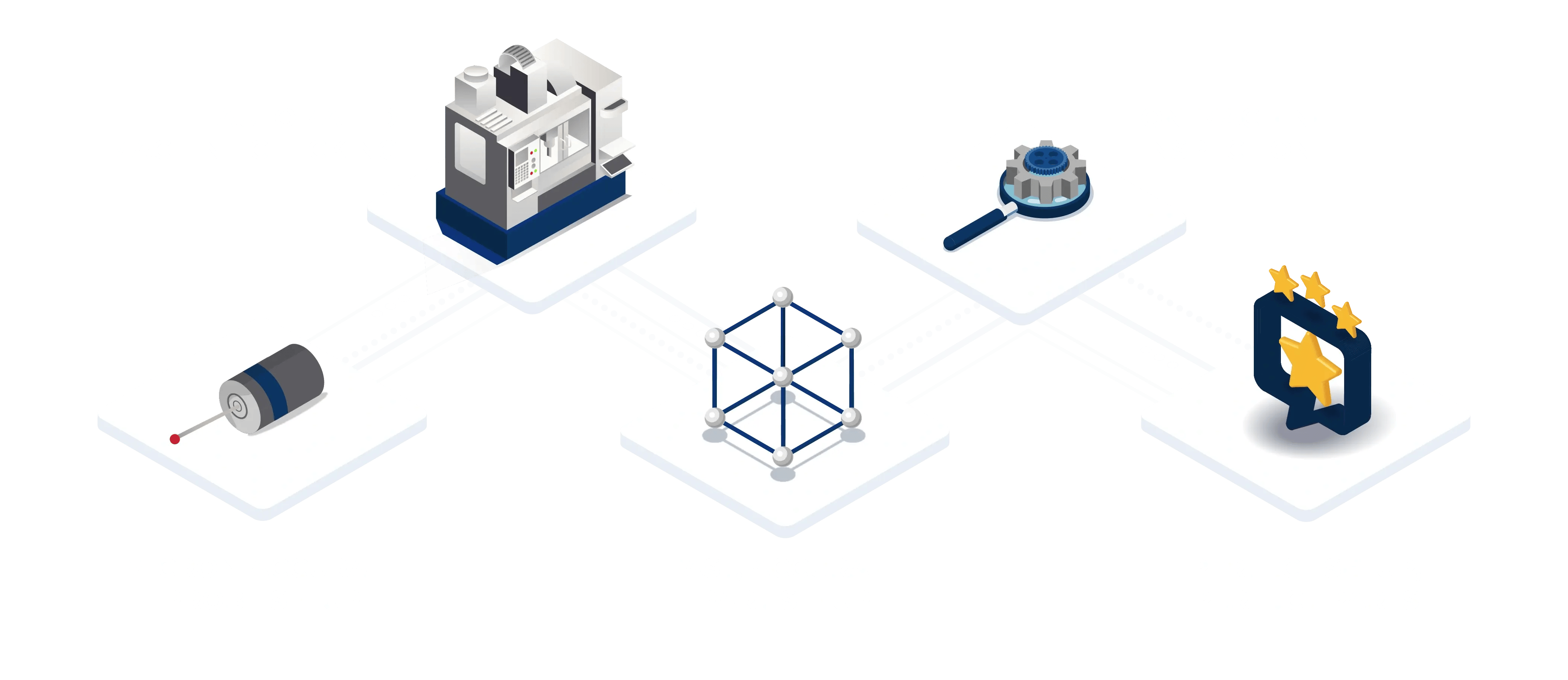
Perfect setup, perfect parts
with MSP PerfectPart
When the whole setup process is accurate and error-free, your production processes will begin producing right-first-time parts. The automation MSP PerfectPart provides also means your production processes will be ready for 24-7 lights-out machining.
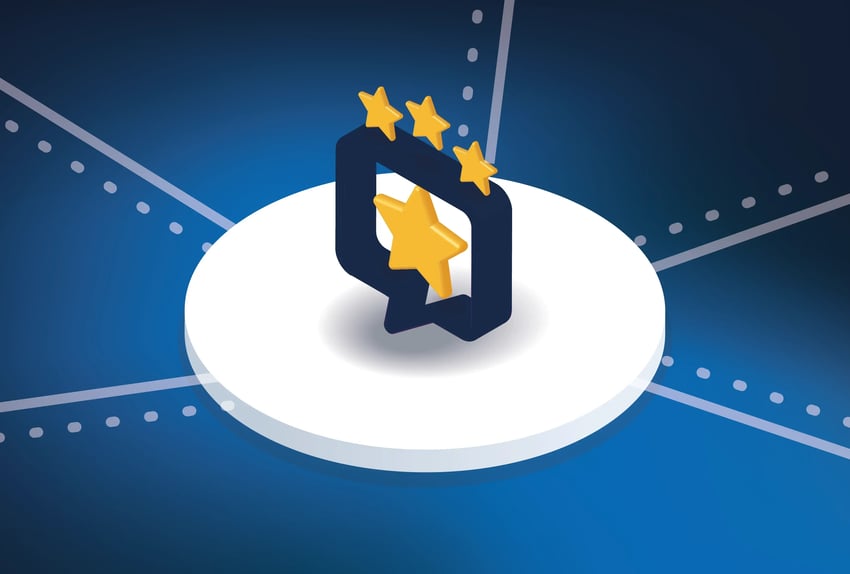
MSP PerfectPart Benefits
24-7 lights-out machining
Speed up setup processes
No manual elements means each process is completed faster.
Minimise machine downtime
Predict maintenance
Anticipate machine failure and schedule maintenance in when needed.
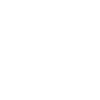
Explain part-to-part variation
Rectify issues across machines to produce parts of uniform quality.
Monitor shopfloor environments
Accurate calibration
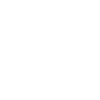
Simplify fixturing
Eliminate scrap
Stabilise schedules
Achieve fixed setup times to keep production schedules on track.
Audit condition of supply
Eliminate CMM backlogs
Don't just take our word for it
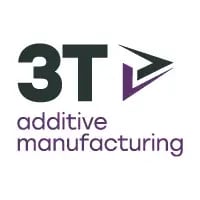
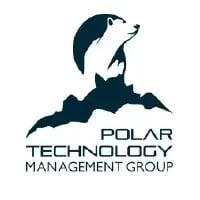
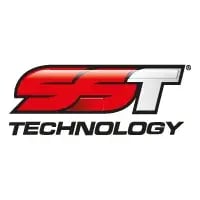
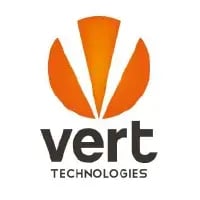
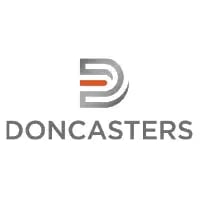
Short relevant title that’s easy to follow
More in-depth information about this, but keep it simple. What to expect, why should they follow the link?
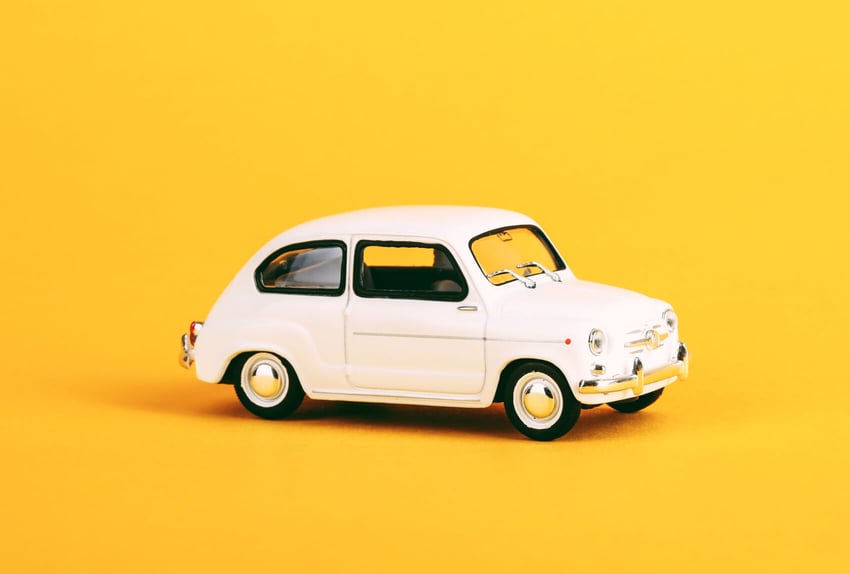
Short relevant title that’s easy to follow
More in-depth information about this, but keep it simple. What to expect, why should they follow the link?
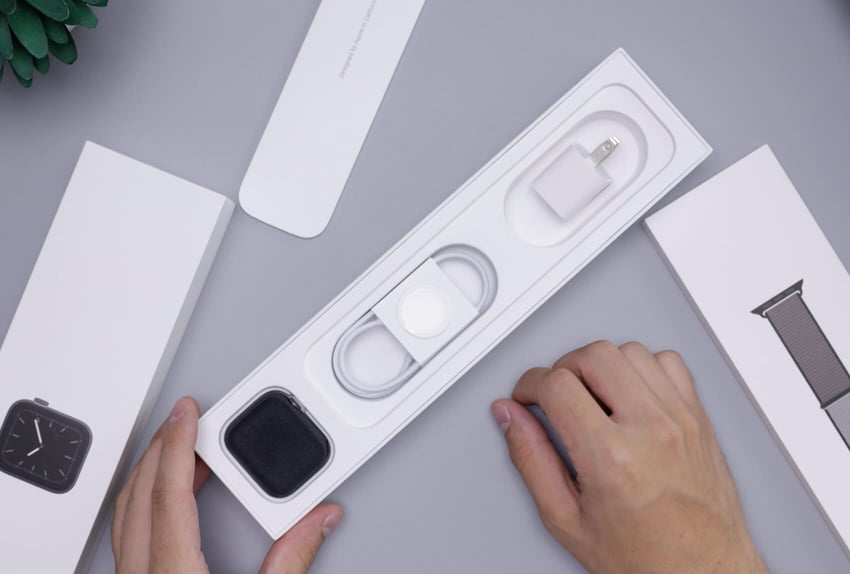
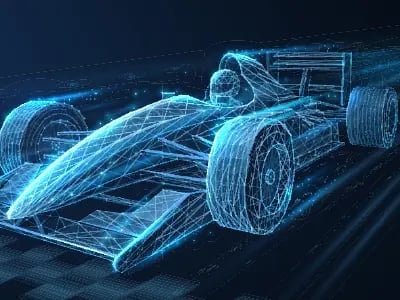
Formula 1 team eliminates part to part variation
Read more here
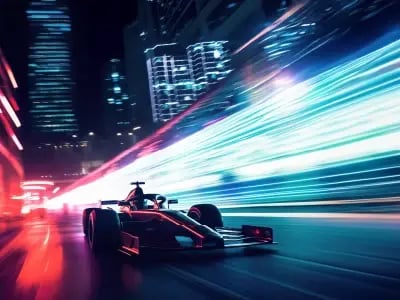
Formula 1 team reduce part setup by 9.5 hours
Read more here
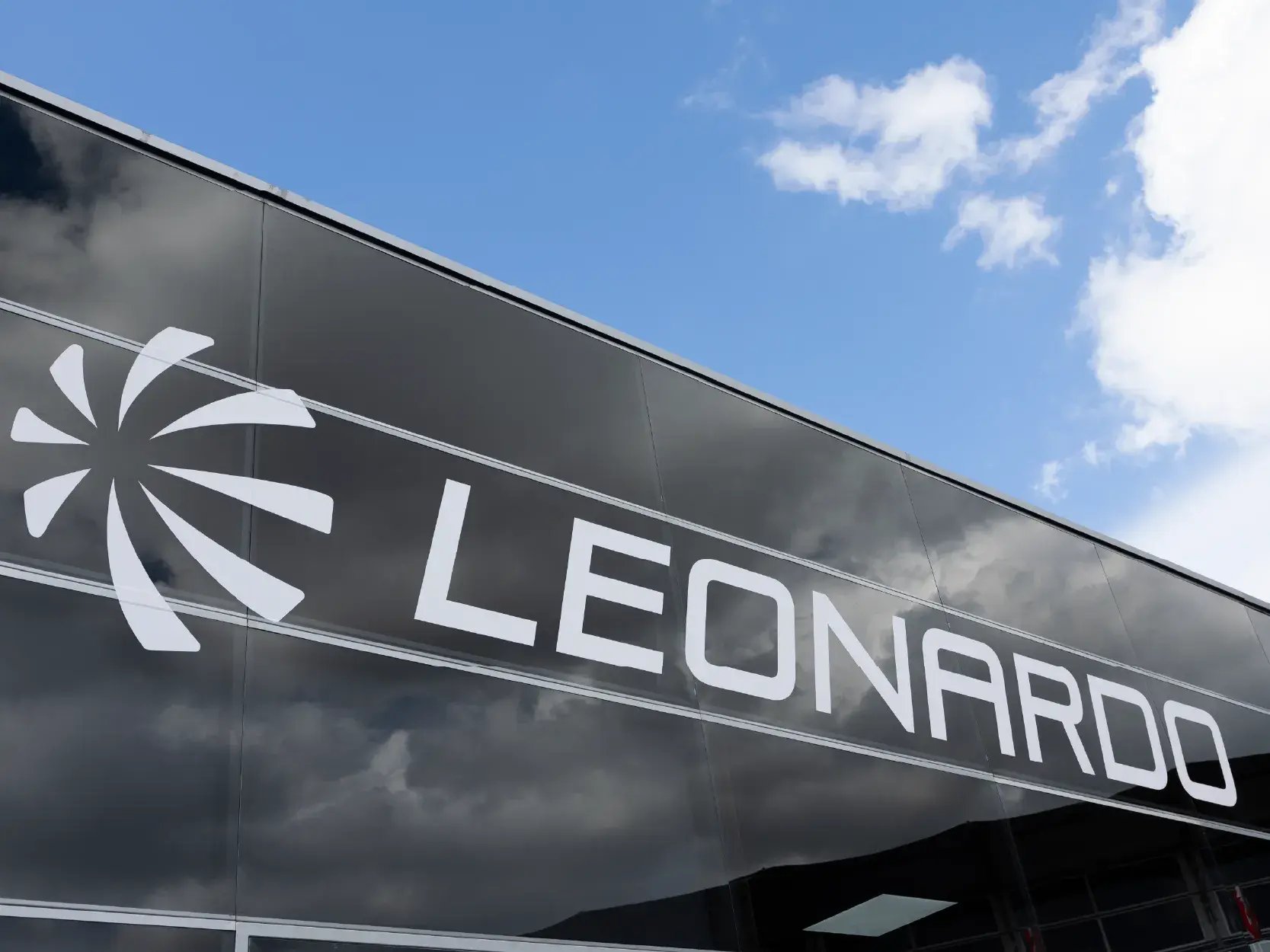
Production time cut from 20 weeks to 3 days
Read more here
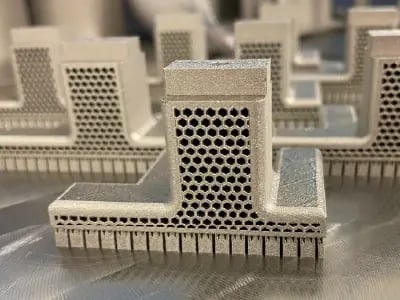
SST now producing 7 times more parts per week
Read more here
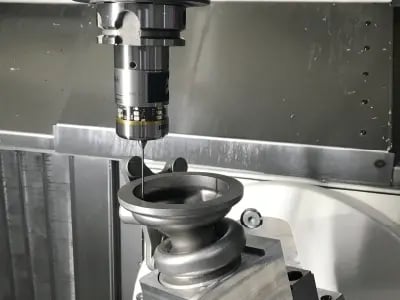
Part setup time cut from 5 hours to 10 minutes
Read more here
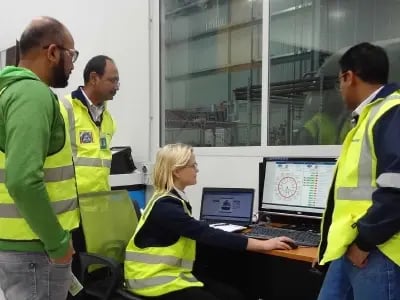
Detailed machine assessments in 96% less time
Read more here
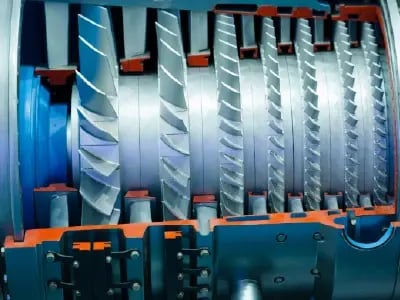
Doncasters increase productivity by 100%
Read more here
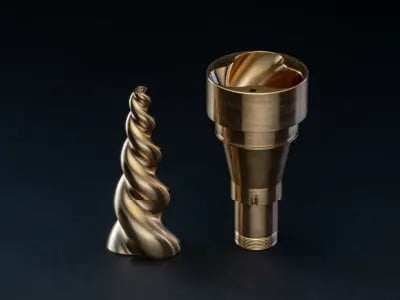
Machine analysis time reduced to minutes
Read more here
Top MSP PerfectPart FAQs
If you purchase the full MSP PerfectPart product suite, you get an end-to-end solution to improve quality throughout your CNC machining processes. It eliminates all potential sources of error from calibration all the way to inspection so you can produce right-first-time parts.
Because of how MSP PerfectPart works, at the same time as improving quality, it also automates your processes, speeds them up, reduces scrap levels and makes shopfloors much more sustainable.
AutoClock: Hardware for micron-accurate and fast probe setup and calibration.
NC-AutoClock: Software for the automated operation of AutoClock and its results. This also allows one AutoClock device to be used per cell.
NC-Checker: Software for machine performance monitoring to understand if your machine is capable of producing parts within tolerance. Creates Benchmark reports.
NC-PartLocator: Software for the automation of the best fit alignment of parts and on-machine part inspection.
Yes! By eliminating all potential sources of errors before any parts are machined or any material is cut, you can have the confidence anything produced will be within tolerance and pass final inspection. For example, errors can occur when the probe is setup and calibrated manually, errors can be present on the machine if there are kinematic or mechanical issues or errors can occur in alignment (either the part hasn’t been located accurately enough or the part differs from the CAD). The products within the MSP PerfectPart suite identify and correct for all of these errors so they don’t affect your parts.
Yes – in many ways! By speeding up probe, machine and part setup processes, sometimes to a mere fraction of the original time, this saves a large amount of wasted energy in time the machine would have been sat idle. And by ensuring right-first-time parts are produced consistently, energy isn’t wasted spent machining parts that eventually have to be scrapped.
MSP PerfectPart also makes it possible to adapt processes to machine near net shapes so manufacturers can create parts using the minimum amount of material possible and make savings as less machining time is needed.
MSP PerfectPart is installed on a standard PC/workstation next to the machine tool on the shopfloor. The PC needs to be connected to the machine tool control either directly or via the company network. No high accuracy CAD is used, so a high-performance PC is not required.
MSP can work with any type of spindle touch probe. We always suggest using the most accurate probe to remove uncertainty from the measurement results. As part of the NC-Checker Benchmark, the Probe Performance check will identify if an upgrade is required for the required part tolerances.