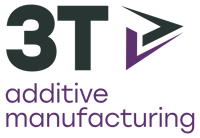
MSP cuts part setup time from 5 hours to 10 minutes for leading AM company
At a glance
A market leader in additive manufacturing in the UK has seen its part setup time reduced from 5 hours to 10 minutes with the adoption of innovative technology from Renishaw plc and MSP.
By automating 3T Additive Manufacturing’s processes, MSP’s products have given the company the confidence to complete the setup and alignment for a full batch of parts in the machine during the day and leave the machine to run overnight. This has enabled 24/7 lights-out production, allowing the company to fully maximise their machine utilisation and machine a whole batch of parts in one day, compared to only one part previously.
Setup Time
Before it would take 5 hours to set up parts using 3T-am's manual alignment process. Now this same process takes 10 minutes - a saving of 96%.
Potential Machine Capacity
3T-am can now use their machines at full capacity - an increase of 157% compared to average weekly usage before.
Machining Capability
3T-am can now complete the setup and alignment for a full batch of parts during the day and leave the machine to run overnight for full 24/7 lights-out automation.
Products used
Background
3T Additive Manufacturing Ltd (3T-am) offers market leading polymer and metal additive manufacturing (3D printing) to a wide range of industries. They offer supply chain solutions providing parts that reduce volume weight, cost and lead times whilst maintaining safety through prototype, development and serial production.
3T-am has grown strongly in recent years and has become a leader in the fast-developing field of additive manufacturing. While traditionally known for its prototype capabilities, more recently it has become established as a serial production company.
3T-am were looking to expand its capability and capacity to meet customer demand. The business had always delivered orders on time, however, due to its meticulous and lengthy setup processes, operators were often required to work unplanned overtime shifts in a bid to fulfill urgent customer orders and meet quick turnaround times.
To ease this pressure, they made significant investments in two five axis mills and a CMM. Despite this extra capacity, each part still required manual setup, and, therefore, created additional demand on their manufacturing personnel to deliver parts on schedule.
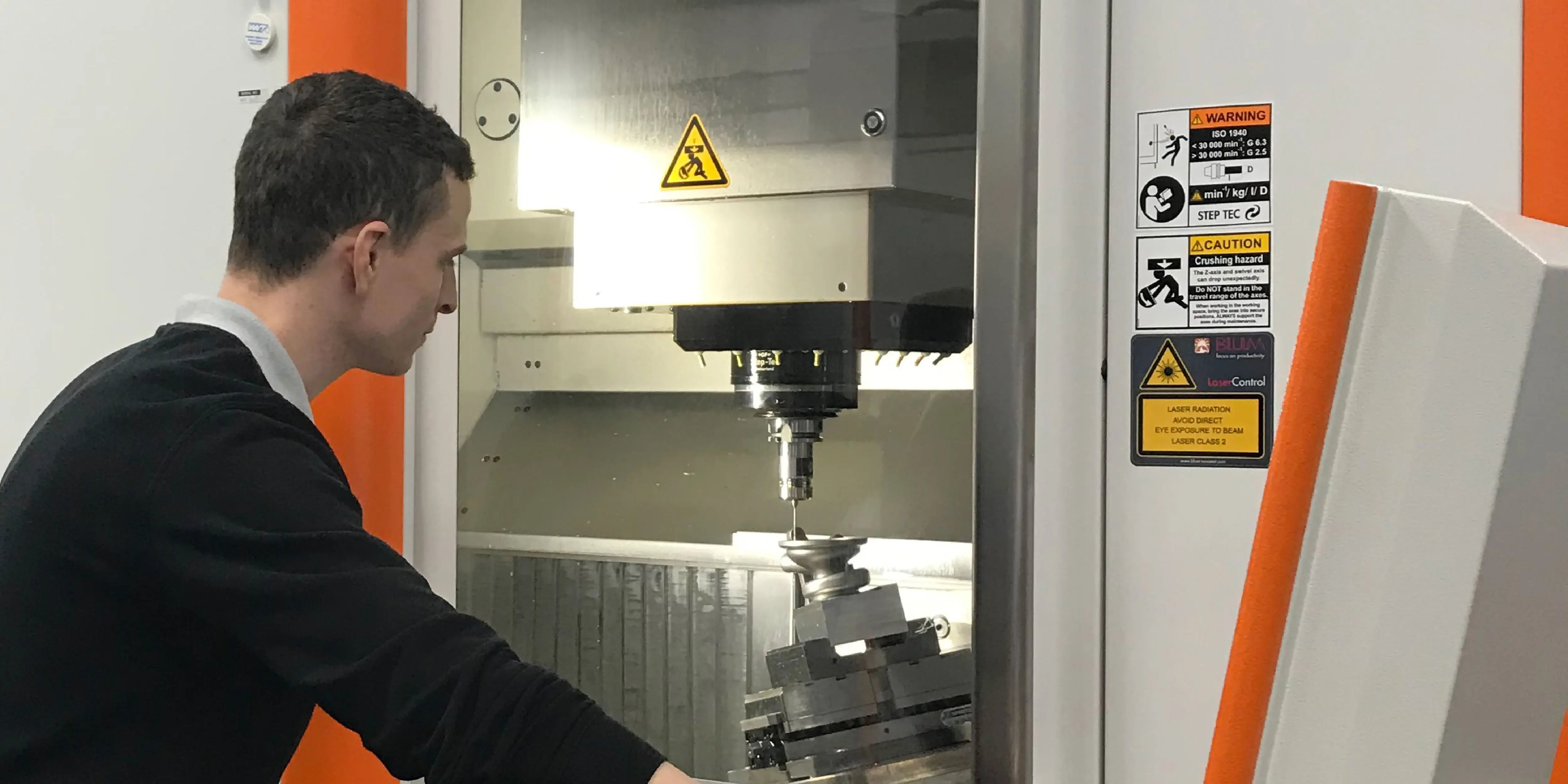
Challenge
3T-am’s ambition was to produce right-first-time parts but realised this would be impossible without automation due to the inherent challenges with Additive Manufactured (AM) parts. Their near-net shape means there is little material to work with; giving no margin of error. They are usually complex shapes with no orthogonal surfaces to locate on making it difficult to achieve accurate alignments. Furthermore, the AM build process can cause parts to distort, meaning its final shape is often marginally different to the CAD model it originated from.
Before MSP’s products were introduced, 3T-am would manually locate the part in the fixture. This was a highly skilled and very time consuming process to ensure the alignment was accurate. Test spotting cuts were made to visually identify positional error. Then either the part was manually adjusted again or updates to the machining program were made. This manual setup process took, on average, 5 hours per part, however, for more complex parts this could sometimes take up a full shift or a whole day.
Once the initial part had been machined, a first article inspection on the CMM was performed before the rest of the batch could be manufactured. For a complex part, this inspection process could check around 67 features (or more) and it would only be at that stage errors were picked up, revealing the setup process needed adjustments and causing delay in the manufacture of the other parts. Even if the inspection process passed, the machine tool had been sitting unused waiting for the inspection result.
Furthermore, the length of the process meant jobs were passed between operators and engineers changing shifts, which resulted in extensive and technical handovers to safeguard the alignments needed on each job. Or for more complex parts, a ‘one job, one man’ method was used to avoid key information being missed, however, this made part manufacture solely dependent on one person and their working shifts, potentially resulting in excessive overtime and pressure for this engineer.
Martin Jarvis, production engineer at 3T-am, said: “Our manual setup was high risk and we had low confidence. We would be nervous when the finished part was taken to inspection as our day’s work could be written off and we would need to do an expensive single part rebuild and fast track it through production to ensure it was delivered on time - that was a problem.”
“Our manual setup was high risk and we had low confidence. We would be nervous when the finished part was taken to inspection as our day’s work could be written off and we would need to do an expensive single part rebuild and fast track it through production to ensure it was delivered on time - that was a problem.”
Martin Jarvis, 3T-am Production Engineer
Solution
3T-am turned to Renishaw PLC and MSP to help reduce setup times, improve quality and automate their processes in order to make full use of their pallet changing system for lights-out production and maximise machining capacity.
Renishaw's OMP600 high-accuracy machine tool probe and software from the MSP PerfectPart suite of products allows 3T-am to identify and correct errors in part positioning and machine performance prior to machining. The OMP600 offers all the benefits of automated job setup as well as the ability to measure complex 3D part geometries and, in combination with MSP's software, automates machining processes and eliminates the potential for human error.
First, NC-Checker assesses the machine tool’s geometric performance to ensure it is calibrated and correct in 5-axis movement. This confirms every aspect of the probe and machine performance is within set tolerances prior to part setup and machining to ensure the parts can be finished accurately.
The part is securely loaded into the machine and NC-PartLocator then measures the part to calculate an accurate best fit alignment in 6 degrees of freedom. The controller is automatically updated to compensate for the discrepancy between the physical part location and the nominal machining program, to ensure the machining path takes place where the real part is. This eliminates the need to carefully fixture and adjust the part manually. Crucially any misalignment errors are automatically removed and the time taken to align or locate the part is significantly reduced.
The same measurements are then used by the software to check the parts condition of supply. It produces a Pre-Machining Inspection Report which shows if there is too much distortion or not enough material to create a ‘good part’ or ‘clean up’ in the areas which are to be machined. This is generated before any machining begins so the part process can be stopped from the outset if any condition of supply errors are present.
NC-PartLocator’s ability to automate part alignment and take measurements at any tool orientation, in any direction, also allows for simple, generic work holding to be used, as the fixture is only required to securely hold the part. This removes the need for expensive bespoke location fixtures and allows the same fixture to be used for multiple parts (where applicable).
At the end of the process, using NC-PartLocator, the part can be inspected on the machine before it is removed from the fixture and a Post-Machining Verification report is produced which verifies the part has been machined within tolerance. This reduces reliance on the CMM, eradicating CMM bottlenecks and gives the ability to automate the inspection process.
3T-am also invested in MSP’s NC-Inspect MODUS to generate the alignment and inspection probing programs for NC-PartLocator to run. This product has been specifically designed to be compatible with NC-PartLocator functionality, making it quicker and easier to create the probing programs. They can be generated offline, away from the machine and can be prepared in advance to limit the amount of machine downtime.
Martin Jarvis said: “Renishaw said MSP’s software could significantly increase our productivity and reduce costs, but I’d heard similar claims from other companies in the past, so I was naturally sceptical - the stark difference with MSP is that it really does what it says on the tin”.
“I challenged MSP to prove their claims in real time as it all seemed too good to be true. I attended Renishaw’s Innovation Centre in Gloucester and presented the MSP engineer with a completely blind test. I turned up with a part which they had no advance knowledge of, and they programmed the part and delivered the promised results before my eyes. When MSP’s products were installed at 3T-am, the MSP guarantee also meant we were making right-first-time parts before their engineer even left site.”
“Now, if we are asked by our customers or supply chain: ‘Can you guarantee quality parts on schedule?’ We can say, ‘Yes with confidence and prove it time and again thanks to MSP’s products'.”
Martin Jarvis, 3T-am Production Engineer
Result
Before Renishaw introduced MSP, 3T-am’s manual part alignment process took, on average, 5 hours per part. Because MSP’s solution automated the alignment process and removed the need to manually adjust the part in the fixture, it has reduced this process to 10 minutes per part – a saving of over 96%.
This automation has also given 3T-am the confidence to complete the setup and alignment for a full batch in the machine during the day and leave the machine to run overnight for full 24/7 lights-out automation.
Martin comments: “We have been able to increase our machine utilisation that could not have been achieved any other way and make the most of the investment in our 5-axis machining centres. We now have the potential to use our machines at full capacity - an increase of 157% compared to our average weekly usage before. We are also now able to machine a whole batch of parts in one day compared to one single part previously”.
This shortened process time and increase in productivity has enabled 3T-am to meet their delivery times effortlessly without the need for unplanned and excessive overtime. The automation has also removed the need to rely on the ‘one job, one man’ system. One shift can be used to set up the parts and, as the software confirms all alignments are correct, the operator can handover to the person taking over with confidence the parts will be machined within tolerance.
The company now use NC-PartLocator’s Pre-Machining Inspection reports instead of lengthy test cuts to confirm the part is aligned accurately and the form of the part is correct before it is machined. This ensures no time is spent machining and adding value to parts that had too much distortion to ‘clean up’ and enables them to start a rebuild earlier, resulting in further time and cost savings. 3T-am also use the Post-Machining Inspection feature to validate their parts after machining while still in the fixture to minimise their use of the CMM and be able to continue production immediately without waiting for final inspection; speeding up processes further.
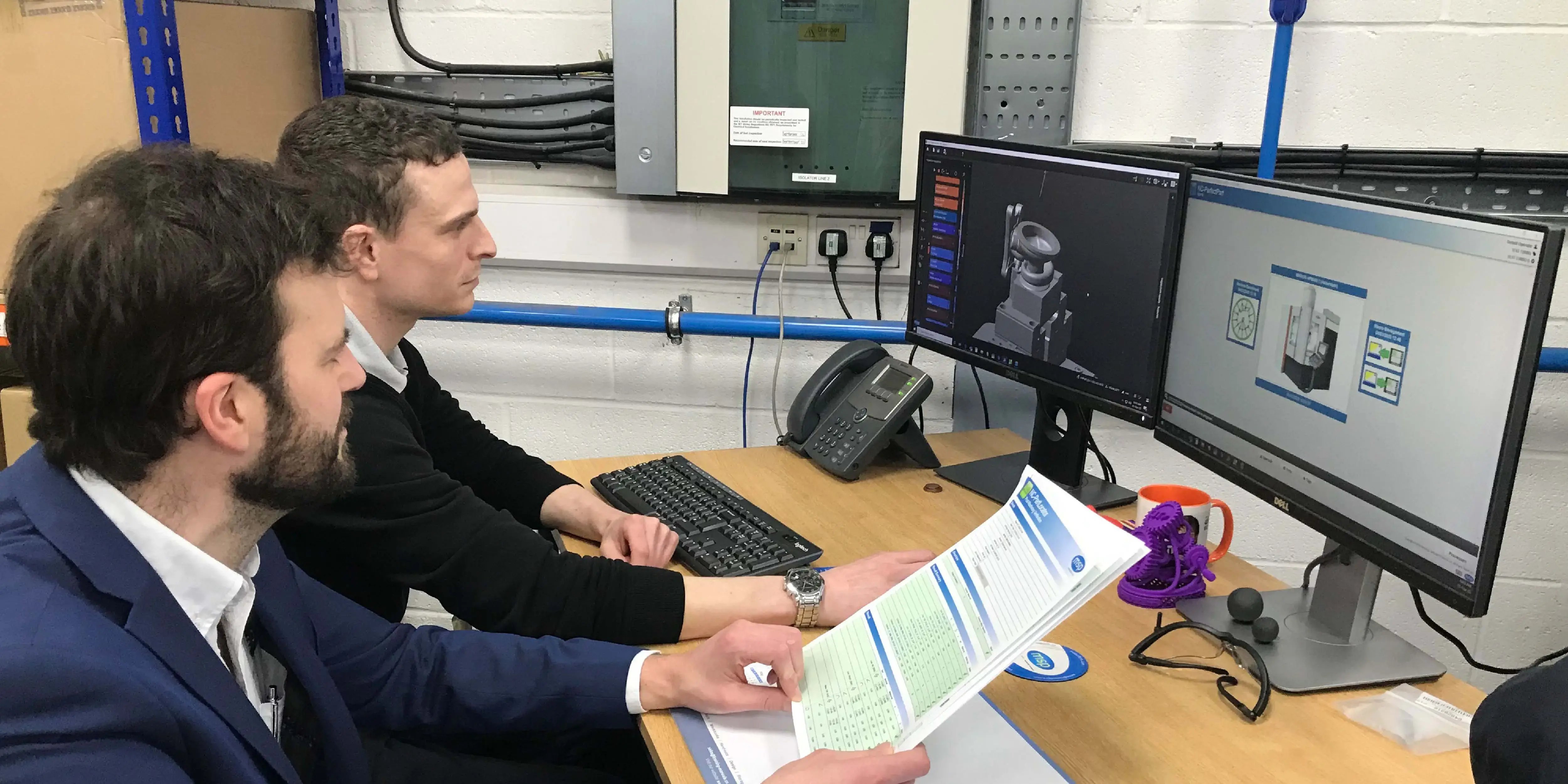
The software’s ability to automatically account for the inherent issues with AM parts gives extra benefits. Martin explains: “Automation has been very important for us. We work within a very fast-moving industry and one where we are always learning - we constantly try and push ourselves. We can now finish parts that are at high risk of distortion and achieve all of the complex alignments or complicated part designs that were so challenging with manual setup. It has given us the ability and confidence to take on more complex work and expand our capability”.
Operator and Programmer at 3T-am, Jon Saunders said: “As well as the great results, we have been very pleasantly surprised by how straightforward MSP’s software has been for us to use day to day. The automation gives us the certainty we always wanted that the parts are going to be right. We started seeing quality results straight away and if we need anything from MSP, the team respond in good time and in a clear, concise and very helpful manner. Their PerfectPart Solution has certainly made our life easier”.
Martin concludes: “The impact has been huge for us in terms of our working practices and the confidence we now have in delivering what we do - it has almost made me want to get back out working on the shop floor”.
Be in a case study.
If you’ve had impressive results and want to be involved in your own case study, we want to hear from you! It’s a great way to shout about the collaboration between our great companies.