Check machine performance
NC-Checker performs a series of checks and shows if your probe and machine are within tolerance (or not) and capable of producing parts accurately. Any errors can be rectified before machining starts so a quality part will be produced every time.
Compare machines
If you have NC-Checker on multiple machines, you can compare their geometric performance. Is your machine as good today as it was yesterday? Does machine A differ from machine B? Has temperature affected performance? Any discrepancies may be causing part to part variation. This helps explain and mitigate varying results so you produce parts of uniform quality.
Perform preventative maintenance
NC-Checker monitors the geometric drift of a machine and produces a 'trend' report which can be used to anticipate machine failure and schedule maintenance while the machine is in tolerance, at a convenient time for production. This avoids disrupting production with emergency call-outs and causing unnecessary machine downtime.
Calibrate the probe in 5-axis
NC-Checker calibrates the probe in 5-axis which allows us to measure parts at any direction, at any tool orientation using a single calibration. This ensures the point is accurate at any orientation. This also means all probing axes are taken into account in calibration, ensuring accurate and good metrology.
Increase in-process quality
Identify errors at the start of your machining process to stop errors being machined into your parts. All checks or benchmarks can be viewed and analysed in real time to understand how your machine is performing at that moment. It is also possible to view archived results and reports if needed.
Check machine performance
NC-Checker performs a series of checks and shows if your probe and machine are within tolerance (or not) and capable of producing parts accurately. Any errors can be rectified before machining starts so a quality part will be produced every time.
Informative | Quality control | Simple
Compare machines
If you have NC-Checker on multiple machines, you can compare their geometric performance. Is your machine as good today as it was yesterday? Does machine A differ from machine B? Has temperature affected performance? Any discrepancies may be causing part to part variation. This helps explain and mitigate varying results so you produce parts of uniform quality.
Accurate | Informative | Simple
Perform preventative maintenance
NC-Checker monitors the geometric drift of a machine and produces a 'trend' report which can be used to anticipate machine failure and schedule maintenance while the machine is in tolerance, at a convenient time for production. This avoids disrupting production with emergency call-outs and causing unnecessary machine downtime.
Predictive | Strategic | Simple
Calibrate the probe in 5-axis
NC-Checker calibrates the probe in 5-axis which allows us to measure parts at any direction, at any tool orientation using a single calibration. This ensures the point is accurate at any orientation. This also means all probing axes are taken into account in calibration, ensuring accurate and good metrology.
Accurate | Good metrology | Simple
Increase in-process quality
Identify errors at the start of your machining process to stop errors being machined into your parts. All checks or benchmarks can be viewed and analysed in real time to understand how your machine is performing at that moment. It is also possible to view archived results and reports if needed.
Cost saving | Accurate | Simple
Product Benefits
Understand your machine
See how its performing. Highlight any errors.
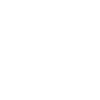
Explain part-to-part variation
Rectify issues across machines to produce parts of uniform quality.
Predict maintenance
Anticipate machine failure and schedule maintenance in when needed.
Compare machines
Minimise machine downtime
Monitor shopfloor environments
Comprehensive testing
Solve problems faster
Prioritise production
Get the machine back into production as quick as possible.
Accurate calibration
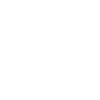
Detect errors
NC-Checker Benchmark Reports
NC-Checker produces simple reports which display the machine's current status. Green for Go. Red for No-Go.
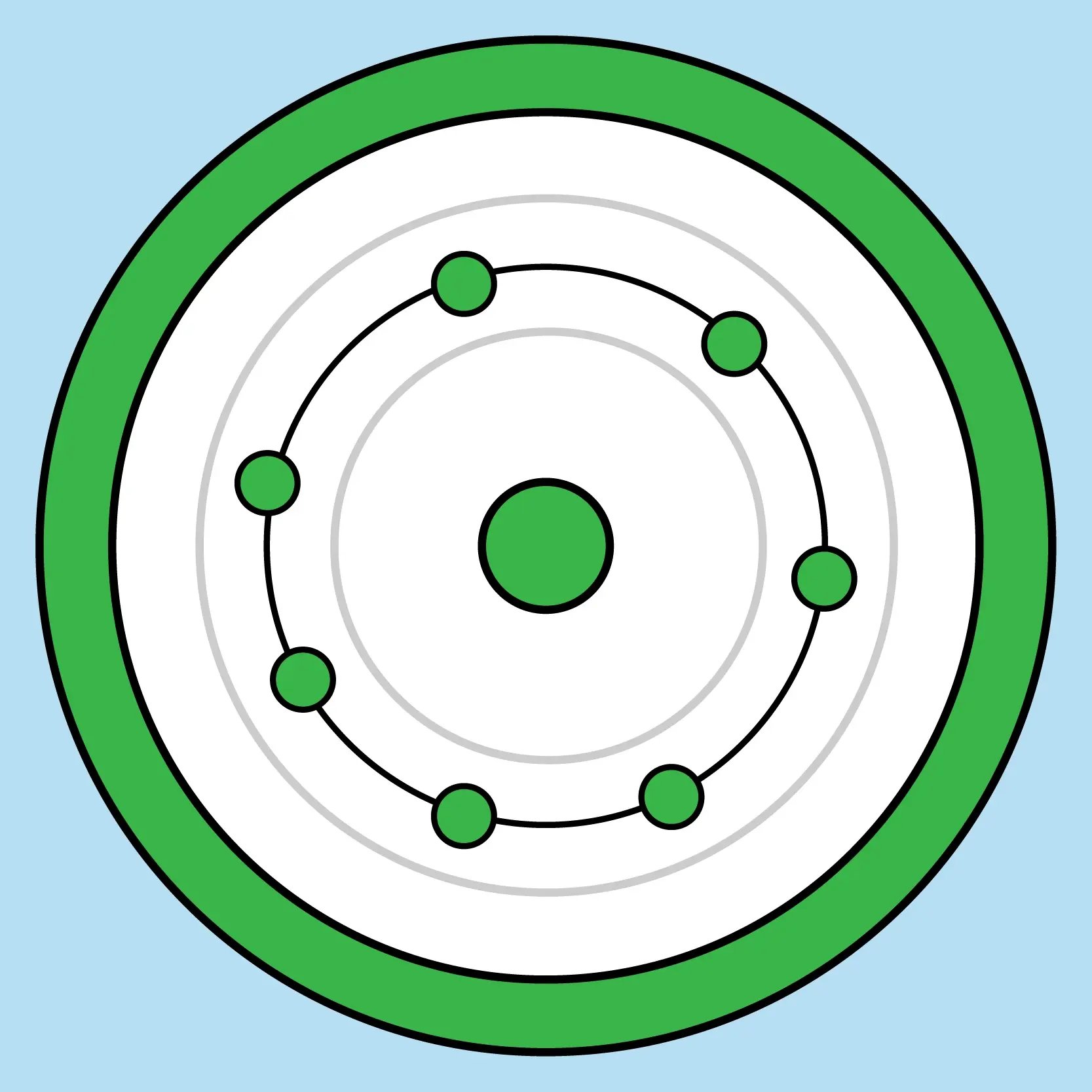
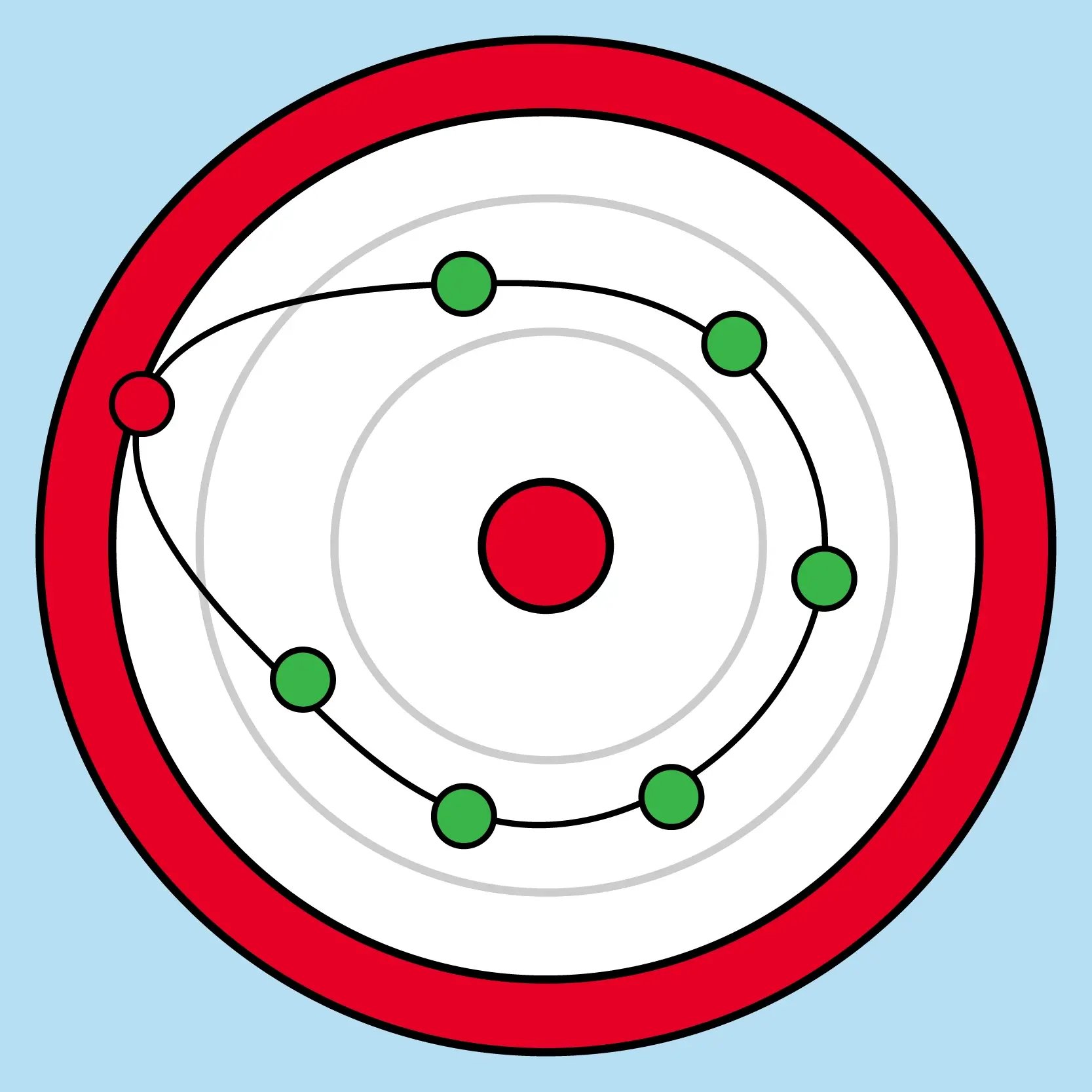
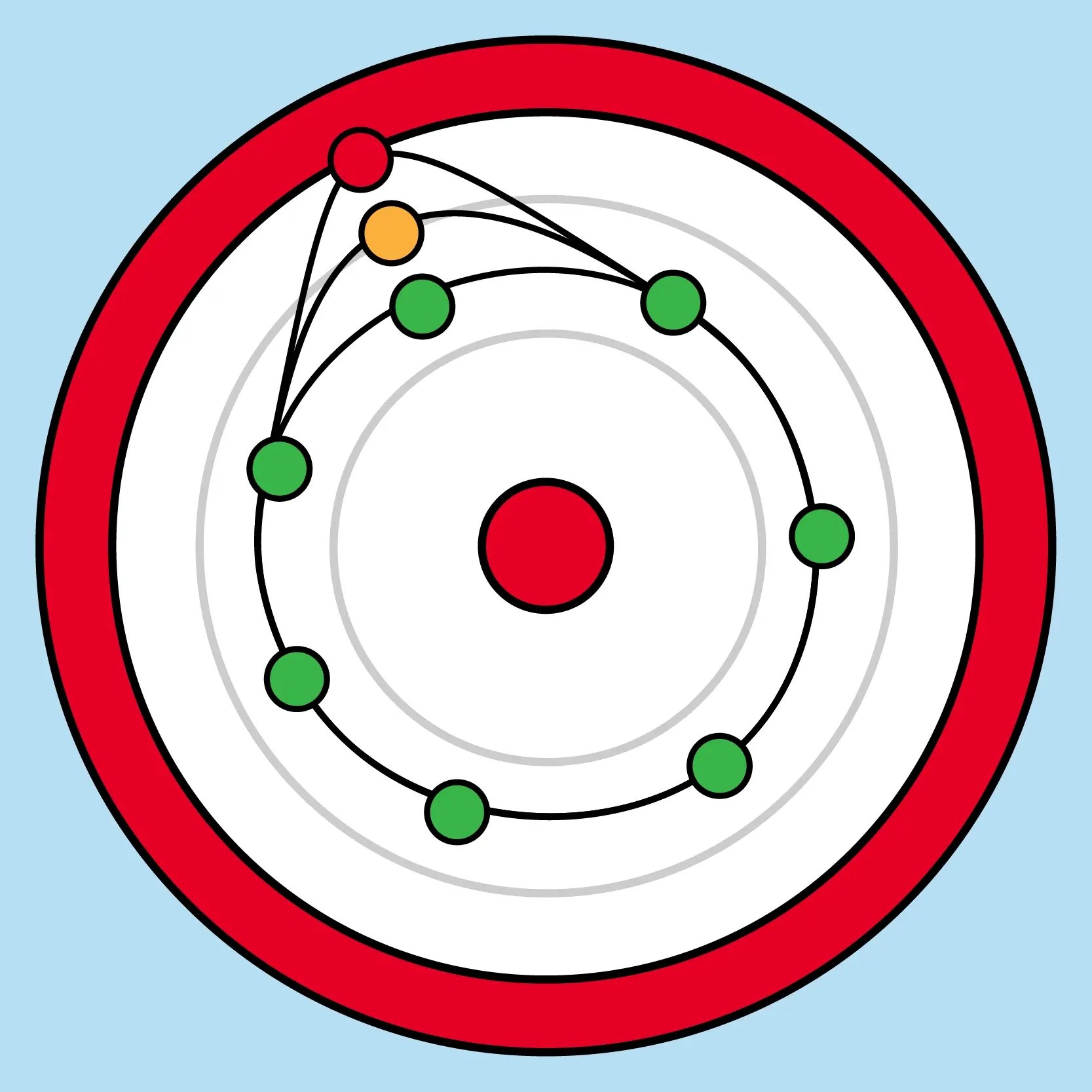
Watch it in action
Learn how to:
Protect your parts from machine errors
NC-Checker highlights any errors before machining starts and allows you to rectify them. Protect your parts from machine errors causing scrap or rework.
Keep your machines in the best condition
Protect your assets and keep your machines to the best condition that they can be.
Remotely review machine performance
NC-Checker's results can be held centrally so you can remotely view how your machines are performing in real time.
Make better budget decisions
NC-Checker gives you the ability to make strategic decisions on how to spend your maintenance and capital budgets based on the different machine capabilities on the shopfloor.
Tender for more valuable work
Demonstrate your machine capability with NC-Checker, giving you the confidence to tender for more valuable work.
Don't just take our word for it
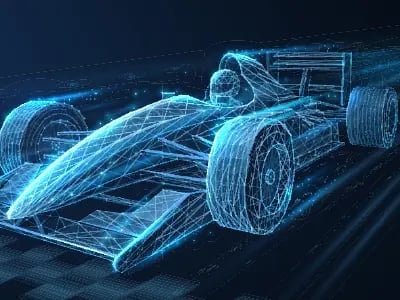
Formula 1 team eliminates part to part variation
Read more here
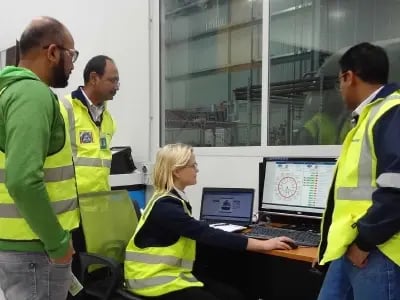
Detailed machine assessments in 96% less time
Read more here
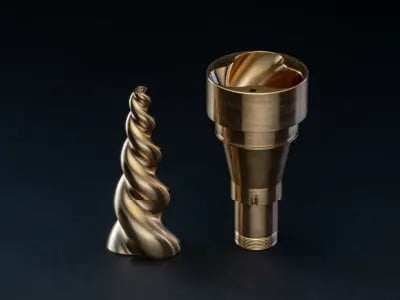
Machine analysis time reduced to minutes
Read more here
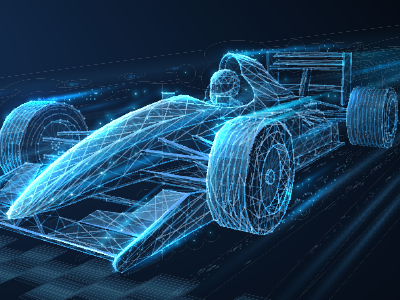
Formula 1 team eliminates part to part variation
Read more here
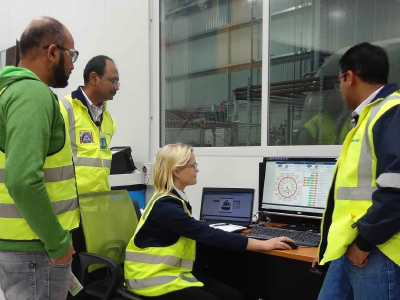
Detailed machine assessments in 96% less time
Read more here
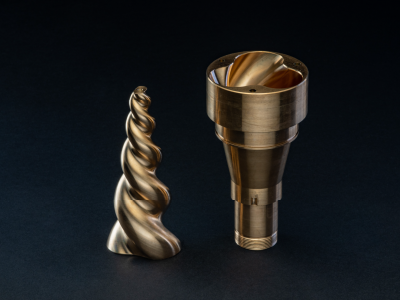
Machine analysis time reduced to minutes
Read more here
Short relevant title that’s easy to follow
More in-depth information about this, but keep it simple. What to expect, why should they follow the link?
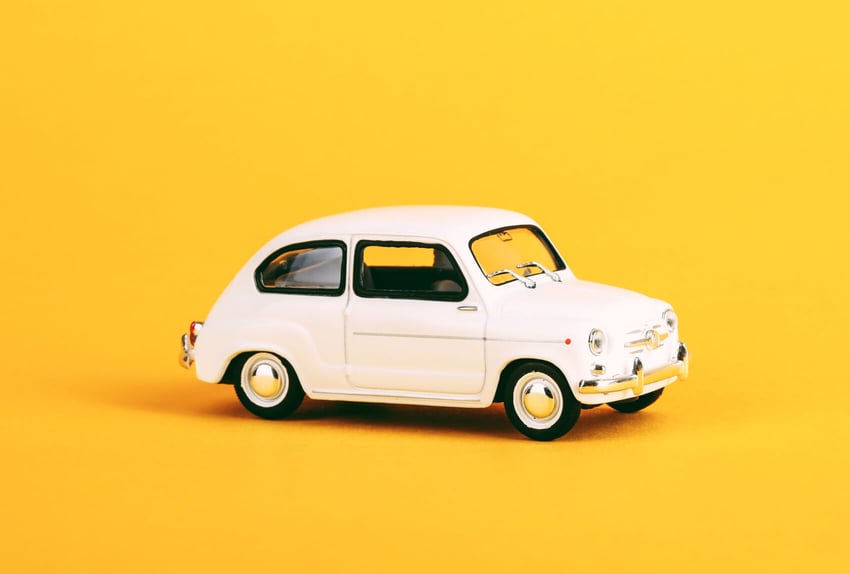
Short relevant title that’s easy to follow
More in-depth information about this, but keep it simple. What to expect, why should they follow the link?
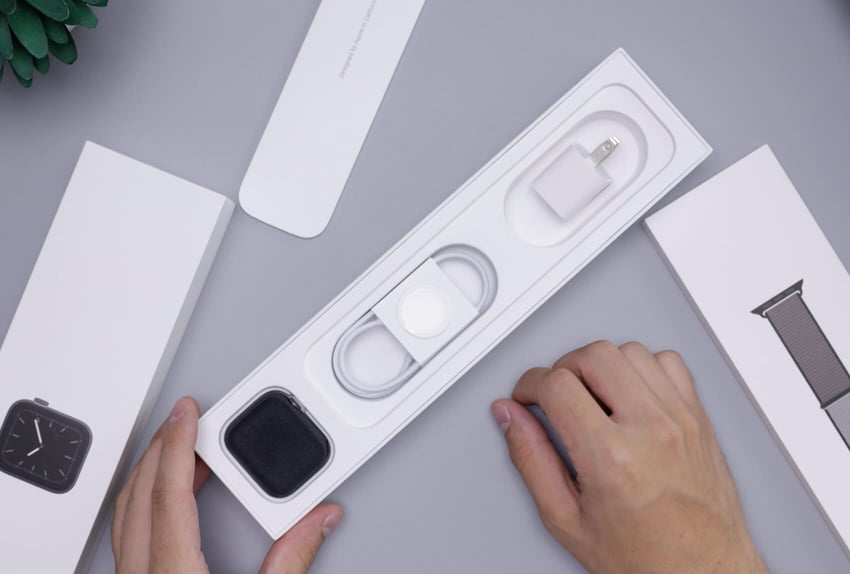
Top NC-Checker FAQs
In a nutshell, NC-Checker shows you if your machine is capable of producing parts to tolerance. What this really means is it shows you if there are any errors present on your machine that could affect part quality. It highlights any mechanical and kinematic errors so these can be rectified before parts are machined.
Not only does it protect your machine and parts from damage but it can also show you masses of information such as the reason behind part to part variation, if changing environmental conditions are affecting machine performance or if the machine has damage following a crash.
The full Benchmark program should be regularly scheduled to ensure a machine error is quickly identified. Initially MSP recommends running the Benchmark as often as possible to understand how the machine performance varies day to day and if any external factors have an impact. After that the regularity is normally based on the value of the parts, i.e. the higher value, the higher frequency.
Yes! We have multiple customers that don’t machine any parts until they have completed an NC-Checker Benchmark because it often uncovers errors on the machine that wouldn’t be found otherwise. If these errors aren’t picked up, this can negatively affect parts and cause them to be machined incorrectly or at sub-optimal quality.
NC-Checker significantly reduces the time it takes to assess the capability of a machine, reducing the amount of energy being wasted while the machine is sitting idle during these checks. Some of our customers have seen the time for these checks reduced from days to hours.
By also ensuring the machine is performing within the required tolerances and has no errors it could pass onto machined parts, NC-Checker also helps save wasted energy and material machining parts that would eventually have to be scrapped.
MSP can work with any type of spindle touch probe. We always suggest using the most accurate probe to remove uncertainty from the measurement results. As part of the NC-Checker Benchmark, the Probe Performance check will identify if an upgrade is required for the required part tolerances.