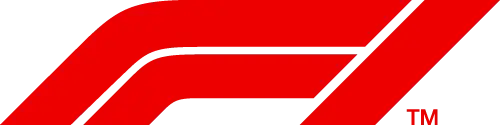
Leading F1 team eliminates part to part variation with help from MSP
At a glance
A leading F1 team contacted MSP to remove or reduce costly errors and eliminate part to part variation which was affecting the company's strict deadlines.
With the help of MSP's NC-Checker, the leading F1 team can now accurately determine machine performance and have eliminated errors and part to part variation.
Part-to-Part Variation
MSP's NC-Checker identified the F1 team's CNC machine tool was drifting out of tolerance. Working with the team's Service Engineers, MSP restored the machine's capability and the issues that were causing the part to part variation were eliminated.
Products used
Introduction
Machine tool diagnostics are an essential step when ensuring your machine tool is running at full capability. Completed daily or weekly, these checks ensure your machine tool is running at the tolerances required for accurate parts.
Before NC-Checker
MSP were called in by a renowned F1 / Motorsport group after they had experienced a series of costly errors which they believed was caused by their fixturing or production process. They were suffering from inconsistency and part to part variation which was playing havoc with their tight deadlines and could not see a solution that was easy to integrate into their existing process. NC-Checker’s machine tool diagnostics were suggested as the solution.
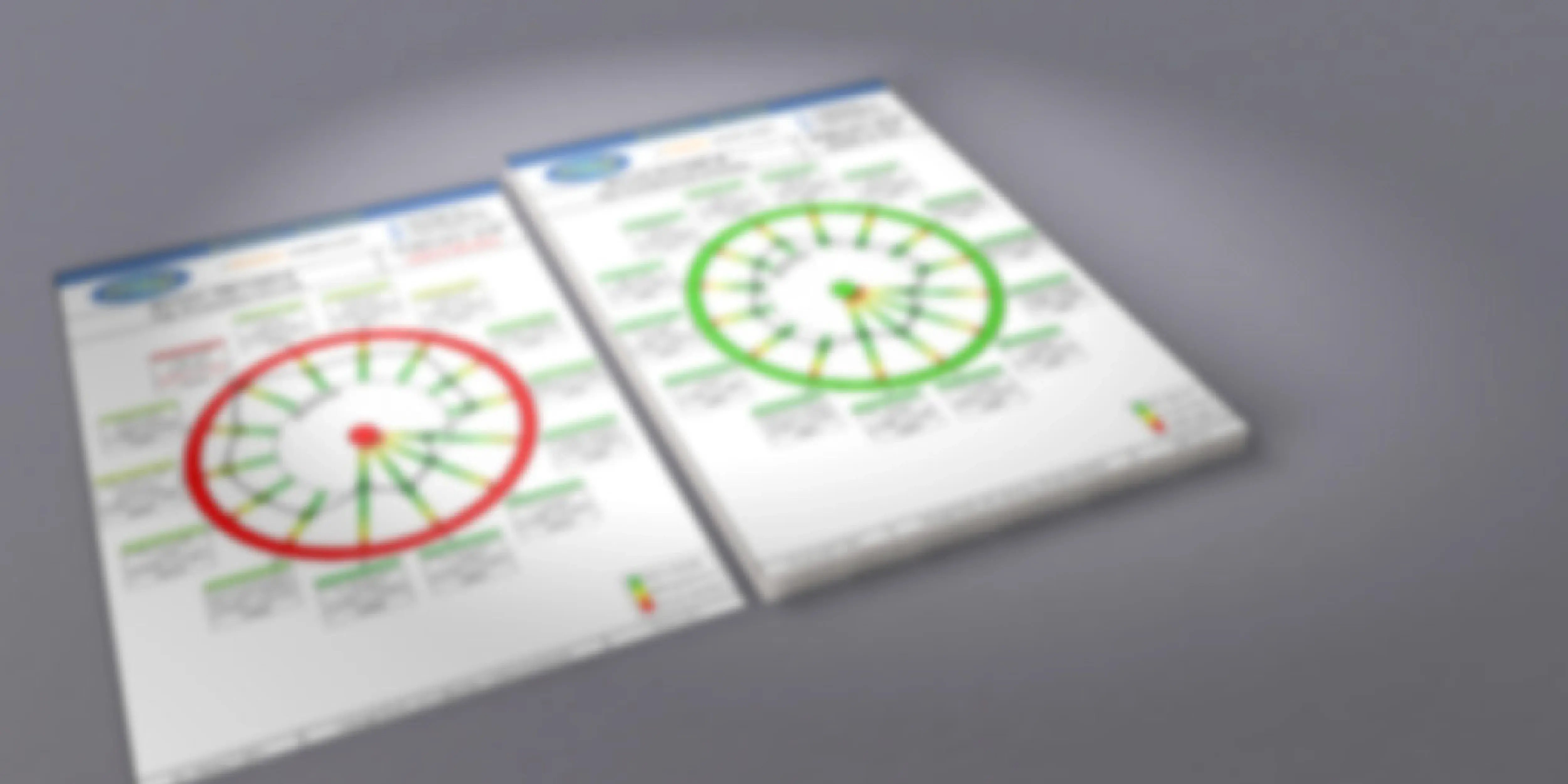
After NC-Checker
MSP conducted a site visit and through the use of a benchmark report, identified that it was the Formula 1 team's machine tool’s integrity that was at fault. MSP was able to create a report that evidenced where the machine was drifting out of tolerance so the company could work effectively with the Service Engineers to restore the machine’s capability.
The customer has now introduced a quality standard against all of their 5-axis machine tools that a regular benchmark (weekly in this instance) will support to ensure that future part to part variation is eliminated.
With the use of machine diagnostics, the customer has the peace of mind and a defined process where they can accurately determine if their machine’s performance is deteriorating. A resulting benefit has allowed them to create a system to predict maintenance which has resulted in a further cost saving as they are no longer reactive to emergency machine down-time.
Be in a case study.
If you’ve had impressive results and want to be involved in your own case study, we want to hear from you! It’s a great way to shout about the collaboration between our great companies.