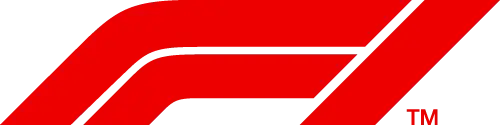
MSP help leading Formula 1 team reduce chassis part setup by 9.5 hours
At a glance
A leading Formula 1 team has reduced its part setup time by an incredible 9.5 hours through using software developed by MSP.
In such a fast-paced sport where every second is vital, the team’s use of NC-Checker and NC-PartLocator from MSP's PerfectPart product suite to automate its part setup process, has reduced the time involved from 10 hours to only 38 minutes.
As well as the huge time saving, productivity has improved greatly and has allowed the team to get their designs through production and onto the track much quicker than ever before, which, in such a constantly-changing and forward-thinking industry, is a significant additional benefit.
Chassis Setup Time
Before it would take 4 hours to set and machine a typical industrial gas turbine nozzle. Now that same part can be probed, machined and checked in under 2 hours.
Part Setup Time
Doncasters' customers are giving them positive feedback as the company has greatly improved their right-first-time pass rate.
Products used
Challenge
A leading Formula 1 team were suffering from long part setup times before machining complex aero components for their car, such as the chassis, nose cone or front wing.
Part set-up has to be accurate as the machining process involves trimming the carbon fibre to tight tolerances and drilling holes at micron precise locations. The company’s manual procedure was extremely time consuming to ensure this accurate part set-up.
Their process involved placing the part in the fixture on the machine, then manually probing it to ensure it had been made correctly and positioned correctly on the machine. The team were probing the parts using manual probing cycles. This involved probing control points one point at a time and recording each result manually.
If any errors were present, the part would have to be moved manually on the machine. Each point would be probed again and each new result written down. This process would be repeated until each point was correct. This was taking up to ten hours and long past some operators shifts. The handwritten results would then have to be collated and emailed to the designer so it could be approved before any machining took place. Due to the length of the process, designers could be receiving emails any time of day or night.
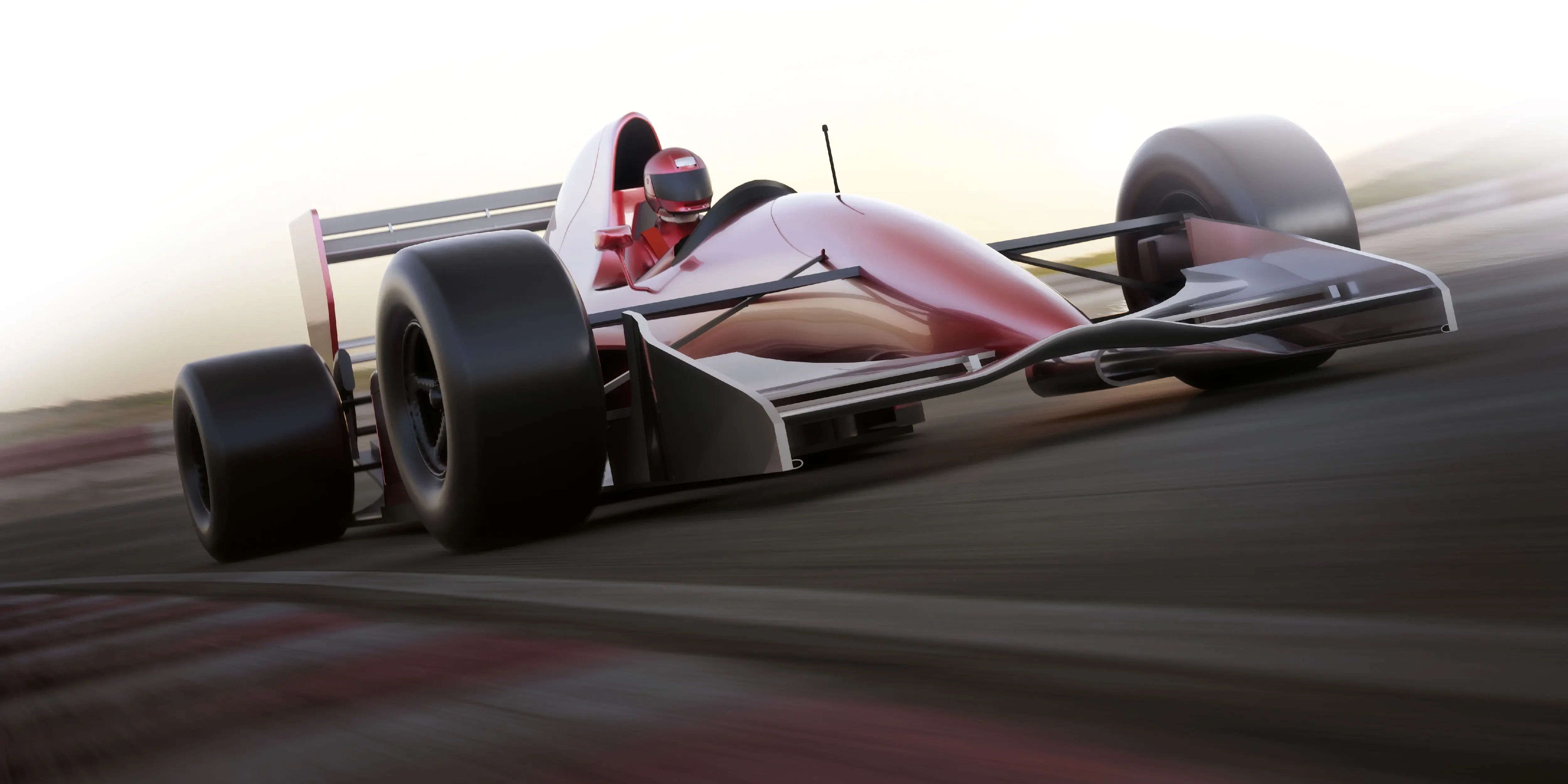
Solution
MSP recognised their NC-Checker and NC-PartLocator software could save a significant amount of time in set-up and give the operators significant control over their process.
NC-Checker makes it possible for operators to identify and remove errors on the machine and make the machine more accurate overall. The software’s benchmark reports also allow them to keep track of the machines performance over time and schedule in maintenance when necessary.
NC-PartLocator eliminates all manual elements from the process. The software automates the probing cycle, allowing all points to be taken at once, with no manual intervention. It produces a print-out report of the probing data, making it easy for operators to send the results to the designers, at a designated time if necessary.
NC-PartLocator auto aligns the machine to the part, eliminating the need to manually move the part around to the correct position. Its Pre-Machining Verification report shows if the part’s alignment is valid and if it has been made correctly and good enough to machine in the first place. This reduces the risk of machining the part incorrectly and having to scrap it afterwards. Chassis production is restricted due to F1 regulations. It is therefore crucial every chassis is correct and zero are scrapped.
Result
Using these MSP PerfectPart software solutions, part setup could be automated and errors could be accounted for by aligning the machine to the part, instead of the other way around. This significantly reduced the team’s set-up time from 10 hours to just 38 minutes each time. This impressive time saving means productivity has improved greatly and has allowed the team to get their designs through production onto the track at record times. As much less time is required on the machine, it is freed up to perform other machining tasks. Furthermore, the fixed set-up time gives operators much more control over machine scheduling and means they can provide accurate delivery times.
Another benefit is the paper trail aspect of the software, as the operators no longer need to record any data manually and, as a result, can send the designer a full probing report effortlessly; at a sensible time of day.
2016 Season - Production of 12 chassis:
Before | After | |
Setup Time | 10 hours | 38 minutes |
Setup for 12 Chassis | 120 hours | 7.6 hours |
Total Saving | 4.5 days |
Be in a case study.
If you’ve had impressive results and want to be involved in your own case study, we want to hear from you! It’s a great way to shout about the collaboration between our great companies.