Share this
Automated Manufacturing Systems: Why Do You Need Automation?
by MSP Marketing on Apr 6, 2023 4:49:00 PM
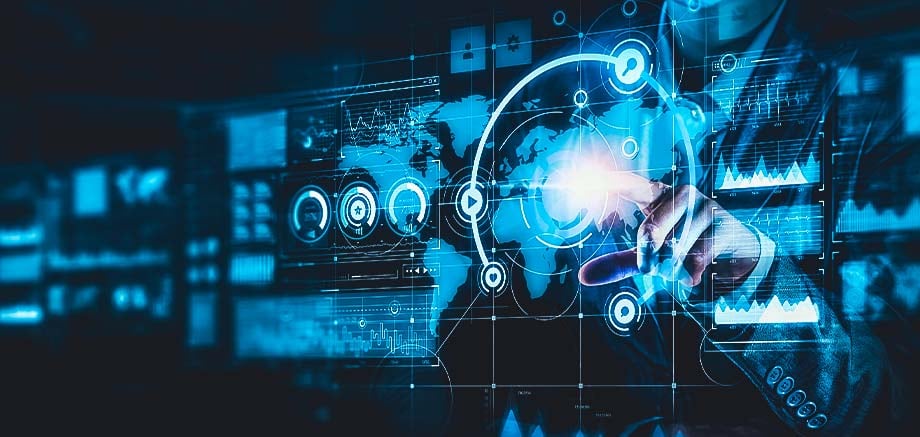
Automated manufacturing solutions involve replacing or supplementing manual processes with technology-driven automated systems.
Any manual processes can be detrimental to the precision, productivity and reliability of a 5-axis CNC machine, therefore, introducing automation into your process as soon as possible will deliver a multitude of benefits to your business and guarantee that you get the most out of your CNC machine(s).
Automation tools also address a wide variety of part process problems common to CNC manufacturing, regardless of the size of company, industry, type of parts, and materials used. Furthermore, automation doesn’t need to involve overhauling or completely replacing your current processes: many automation tools can be integrated with your existing equipment to minimise disruption, leaving your core processes largely the same but significantly improved.
So, how could your business benefit from automated manufacturing systems or technology?
Increased productivity: Automation is key to boosting productivity levels, as automated processes take significantly less time to complete and can free up your operators so they can work on more productive or business-critical/ strategic tasks. Automation gives you greater flexibility over your production schedules without compromising on quality. For example, automation enables your machines to run 24/7, ‘lights-out’ production, making it possible to run them outside of scheduled operator shifts or during periods of operator absence. And if part setup is automated, the production cycle becomes quicker, and more parts can be machined at the same time – reducing the total cost of production as well as increasing output volume. An example of this is additive manufacturing company, 3T-am, who were able to introduce 24/7 lights-out machining to their shop floor with automation and went from machining one part per day to machining a whole batch of parts in the same time.
Improved quality: The main problem with manual processes is their ability to introduce human error and affect accuracy and reliability. In CNC manufacturing, these errors often manifest themselves onto machined parts and cause failures in final inspection. This results in parts needing to be reworked or scrapped. In advanced manufacturing, and especially on 5-axis machine tools, these manual processes include probe setup and part alignment which, if not performed accurately, will cause parts to be machined out of tolerance. Automating these processes eliminates any error and ensures parts will come off the machine right-first-time; every time.
Increased safety: Any CNC manufacturing process that has manual elements will require an operator to enter the machine volume at some point. This poses serious health and safety risks and could potentially be damaging to your business if things go wrong. In contrast, automated processes allow for completely closed-door machining. Operators can press a button on the controller to set processes away safely and with little to no risk to themselves.
Specialist knowledge and more confidence: Automated systems can also often provide additional information about the manufacturing process. For example, manual processes are unable to alert you in real time if your CNC machine is underperforming or if a part will be machined out of tolerance – in the same way automated systems can. This valuable insight stops bad parts from being made, boost profits, and can significantly boost confidence on the shop floor because the risk of machining bad parts is reduced to a minimum. Because automation gives you better control over your machining capabilities this in turn deepens your knowledge about which machines you can use for different applications, which processes are right for each job, and the reasons for part-to-part variation across machines. This equips you to make informed supply and production decisions to lower costs and improve overall productivity.
Increased sustainability: The increased precision that comes with automation reduces scrap and wasted material. Automated part setup technologies can also improve your production line’s energy efficiency by reducing idle and non-productive time. With the ability to carry out more complex work in-house comes a reduced dependency on outsourcing, which cuts the cost, time, and emissions involved in shipping parts back-and-forth.
Automated manufacturing – not as scary as it sounds!
Automated manufacturing doesn’t have to be daunting. MSP can help you introduce automated systems into your CNC machining processes without replacing your existing processes or equipment.
This case study explains how we worked with SST Technology to automate processes, streamline production, improve quality, and lower production costs.
To find out more about the benefits of the MSP PerfectPart suite of products, including AutoClock, NC-Checker and NC-PartLocator, please get in touch.
Or download our guide below.
Share this
- August 2025 (1)
- June 2025 (2)
- April 2025 (1)
- March 2025 (2)
- January 2025 (1)
- November 2024 (1)
- April 2023 (2)
- December 2022 (2)
- July 2022 (1)
- May 2022 (4)
- November 2021 (1)
- October 2021 (1)
- September 2021 (2)
- January 2021 (1)
- December 2020 (1)
- December 2018 (1)
- August 2018 (1)
- August 2017 (1)