Share this
New collaborative project aims to transform part alignment in the CNC manufacturing industry
by MSP Marketing on 9:16 AM on December 11, 2023
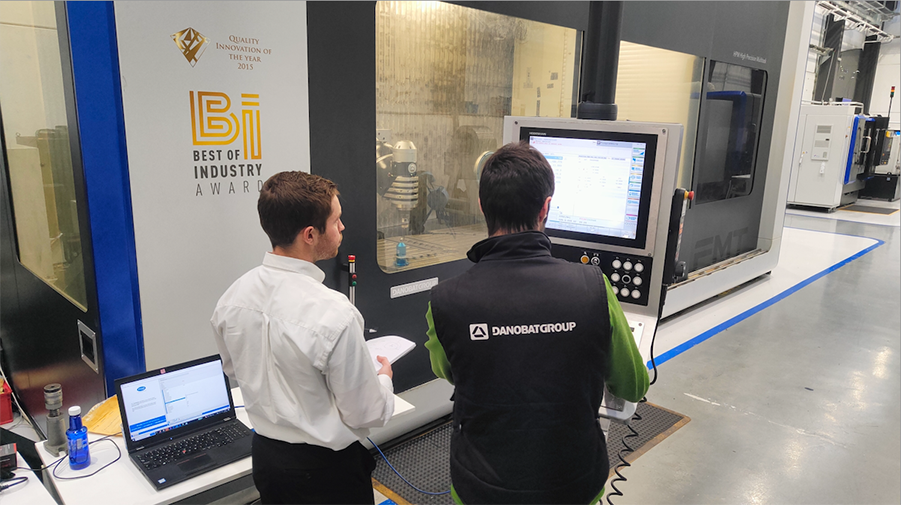
MSP has been involved in an exciting new project to deliver a high-range measurement and alignment system by combining metrology, 5-axis probing and photogrammetry to create a fast and accurate part setup solution.
The TACCO project, funded by EIT Manufacturing, is a collaboration between various companies and research facilities, including MSP, IDEKO, Renishaw and Politecnico di Torino.
MSP has been working with these companies since last year and, recently, MSP PerfectPart Technical Lead, Laurence Reeves, went to IDEKO’s facility in Elgoibar, Spain to further develop the alignment solution and drive this project forward.
Both MSP and IDEKO already provide their own solutions for accurate and automated part setup to deliver zero-defect CNC machining and this collaboration will strengthen each company’s respective expertise to create a solution that will have a massive impact on their customers and on the CNC manufacturing industry as a whole.
MSP’s expertise in metrology and 5-axis probing is being called upon for this project. This expertise has already been central to creating MSP’s PerfectPart suite of products which include AutoClock, NC-Checker and NC-PartLocator. Used in end-to-end CNC machining processes, the products provide automated and accurate probe setup, automated CNC machine tool health checking and automated and accurate part setup.
IDEKO developed solution, VSET, is a measurement system based on 3D vision and photogrammetric technology which is used to align extremely large parts that can’t be aligned or inspected in conventional ways.
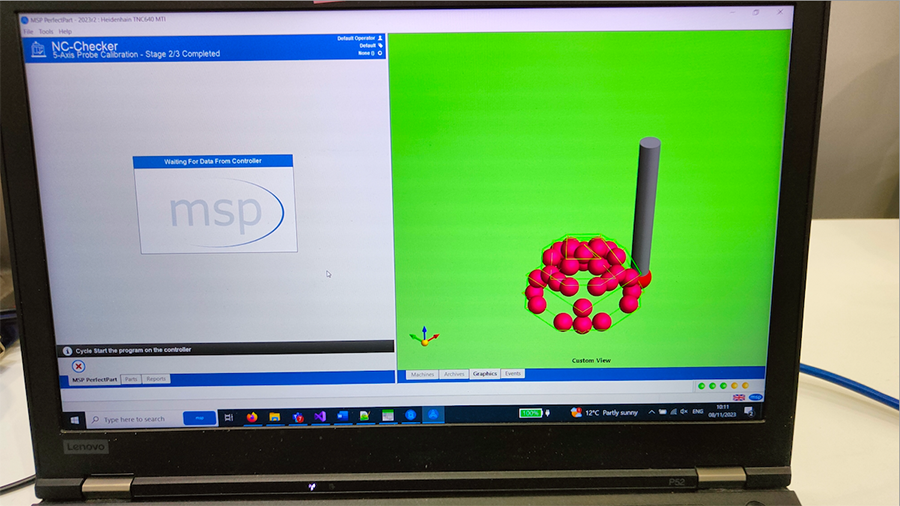
This project will transform the process of generating part alignments within the CNC manufacturing industry. Pictured: MSP's NC-Checker.
Whereas IDEKO’s solution is based on photogrammetry to create part alignments, MSP’s product works by using 5-axis probing to generate a 6-axis best fit alignment and automatically uploads this to the machine controller. It calculates any discrepancy between the part’s location and the machining program to ensure the part will be machined perfectly with zero defects.
Laurence said: “Being involved in this project is really exciting. It’s a great chance to learn from other companies and develop something ground-breaking for our respective customers. Our aim is to offer automated alignments to new markets and, for existing markets, make part alignments even more accurate. Achieving zero-defects in manufacturing is something we’re all passionate about and knowing we’re advancing further in this area is fantastic”.
The full list of partners working on the TACCO project are: MSP, IDEKO, Renishaw, Politecnico di Torino, Mondragon, BBM Group, Dr. Matzat & Co. GmbH Soraluce and WWR.
By working together on this project and applying each other’s strengths, generating part alignments within the CNC manufacturing industry will be transformed and towards a more advanced and sustainable solution for this stage in the machining process.
For more information about IDEKO, visit this page.
For more information about the TACCO project, visit this page.
Share this
- May 2025 (1)
- February 2025 (1)
- December 2024 (2)
- November 2024 (1)
- September 2024 (1)
- May 2024 (1)
- December 2023 (2)
- November 2023 (4)
- October 2023 (2)
- September 2023 (1)
- August 2023 (1)
- July 2023 (2)
- June 2023 (2)
- May 2023 (1)
- April 2023 (1)
- March 2023 (2)
- February 2023 (2)
- December 2022 (1)
- November 2022 (1)
- September 2022 (1)
- July 2022 (2)
- May 2022 (1)
- January 2022 (1)
- October 2021 (1)
- August 2021 (1)
- March 2021 (2)
- February 2021 (1)
- September 2020 (2)
- May 2020 (1)
- March 2020 (1)
- January 2020 (2)
- December 2019 (1)
- November 2019 (1)
- October 2019 (3)
- August 2019 (1)
- June 2019 (1)
- May 2019 (1)
- April 2019 (2)
- March 2019 (1)
- February 2019 (3)
- December 2018 (1)
- October 2018 (1)
- September 2018 (1)
- August 2018 (1)
- July 2018 (1)
- June 2018 (1)
- May 2018 (1)
- April 2018 (1)
- October 2017 (1)
- August 2017 (1)
- July 2016 (1)