Share this
MSP has found ‘Stronger Together’ isn’t just a catchphrase
by MSP Marketing on 4:05 PM on May 13, 2020
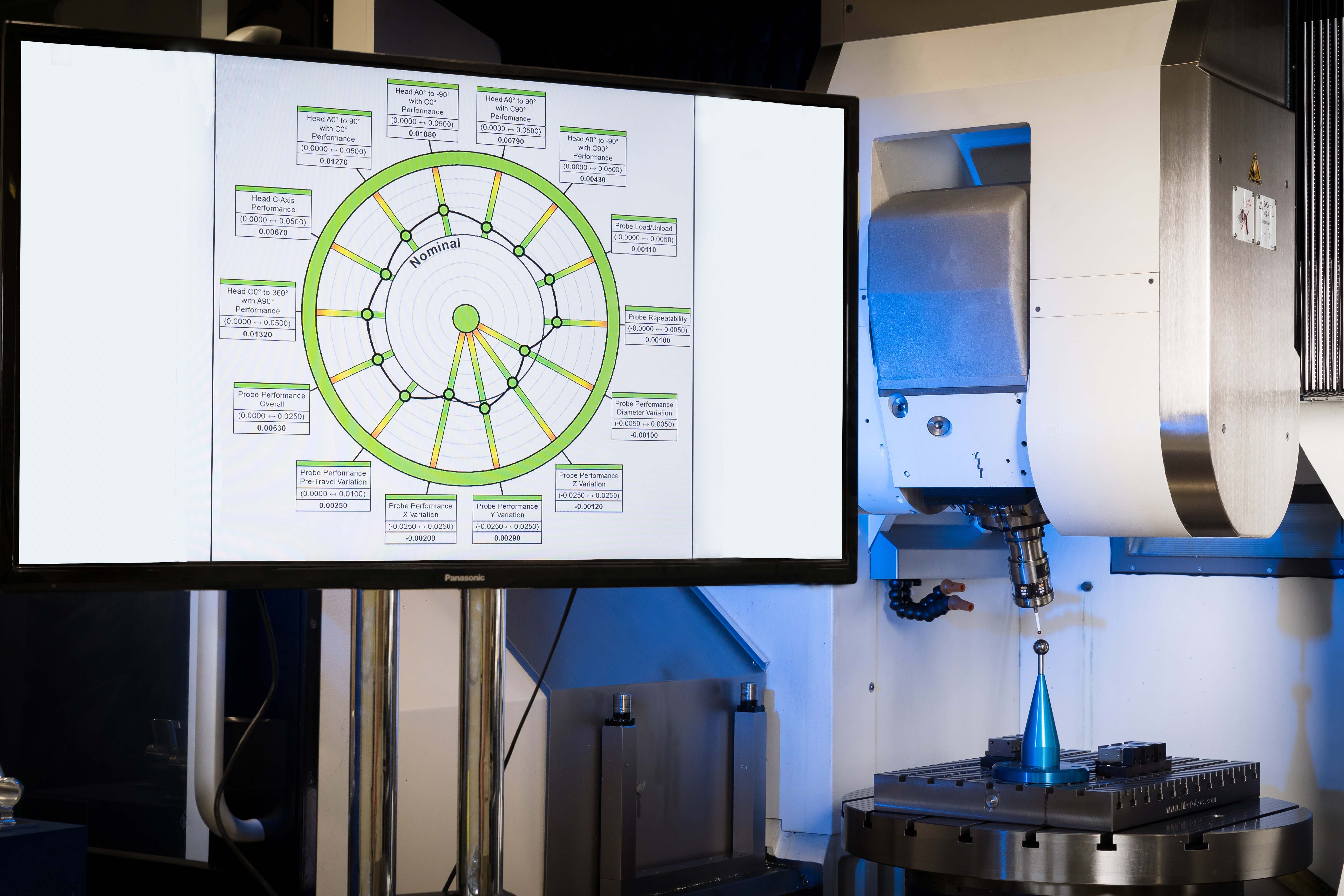
MSP has been adapting its products and services to ensure customers can keep up production in the current climate.
MSP advises global manufacturers on the automation of each stage of their production cycle and guarantees that perfect parts are produced, every time. MSP assesses the CAD design, fixturing, calibration, condition of supply and probing routines, right up to inspection - highlighting and removing errors throughout.
During the COVID-19 crisis, the company has found their ability to offer remote support has been a lifeline to customers who have needed to take advantage of MSP’s programming and machine-checking expertise. With many key personnel unavailable in production facilities, MSP’s engineers have been in high demand.
Investing in more than just a product
Due to recent changes in their process, a UK Tier 1 manufacturer recently contacted MSP for remote programming support. Their programs were being output with a new post and they wanted MSP to audit the code to ensure it was still correct. After analysis of the program, MSP’s engineer found and corrected multiple errors which would have had a detrimental effect within the machining process. He was also able to advise the company how to adapt their use of NC-PartLocator, maximise functionality, and streamline their programs from four programs to one. This saved vital time and programming effort - crucial during a time when their resources were limited.
A Tier 2 manufacturer in the Republic of Ireland had previously invested in NC-PartLocator to allow on-machine inspection as the parts couldn’t be measured on a CMM due to their size. After recently winning a tender within an essential supply chain, but suffering staff shortages, the customer approached MSP for programming support and realised they had invested in more than just a product. By applying their knowledge of alignment strategies to create the necessary probing programs, MSP’s engineers were able to ensure the customer’s operator could set production going - with full confidence the part would be machined correctly.
Making MSP part of your team
Due to the pandemic, MSP has struggled to deliver their services onsite and so has worked hard to adapt their installation processes to deliver them remotely - allowing customers to continue to fulfil their orders. Furthermore, due to staff shortages, MSP has seen several of its customers recruiting external contractors to keep critical projects in production. This creates complications with contractors having to get up to speed with unfamiliar production processes and them not understanding how to get the best out of the company’s investment in MSP’s solutions.
MSP’s engineers have worked with multiple customers over the last few weeks to support their external contractors step by step - delivering the post edits required for the machining programs, creating probing programs, and enabling the operator to press ‘Go’ and keep production going. MSP has also shared training documents and videos so that both contractors and operators know what to do when the production cycle starts. Manufacturers have relied heavily on MSP’s engineering team and have admitted to using them as ‘one of their own’. This has ensured that MSP’s customers have maintained their production throughout the crisis, despite staff shortages, reliance on contract personnel and reduced working hours.
Keeping your machine in production
MSP has also helped customers in the motorsport industry who are suffering dramatically during the pandemic. One customer contacted MSP’s support team for help with interpreting their NC-Checker Machine Benchmark Report results. As part of MSP’s solution, this important tool displays if a machine is capable of producing parts within tolerance. Often when a machine is showing it is out of tolerance, the instinct is to take it out of production to prevent further mechanical damage. In normal circumstances, the customer would have flown in an external engineer from Germany to solve the issue, but instead they requested MSP’s expertise.
The NC-Checker Machine Benchmark Report distinguishes between kinematic and mechanical errors. The customer wanted reassurance that their understanding of the report results were correct - the problem was kinematic and they did not need to request an engineer from Germany. MSP’s engineer confirmed their understanding was correct and that the Report was showing their Rotary Axis tests were displaying large kinematic errors. This indicated the mechanical performance of the axes were in good condition but the machine parameters relating to the kinematic point of rotation and pivot required adjustment.
Amanda Tait, MSP’s engineer who was supporting the customer, explains:
“The adjustments could be made by the customer themselves, meaning the external OEM was not necessary. Following our 20-minute phone call, their machine was back in production and making parts within 40 minutes. Our advice was priceless and saved the company approximately £20,000 in downtime, lost production and lengthy waits for a maintenance visit. The production manager admitted to being in disbelief that a phone call could have such a positive impact on their production, but the proof was in the finished parts”.
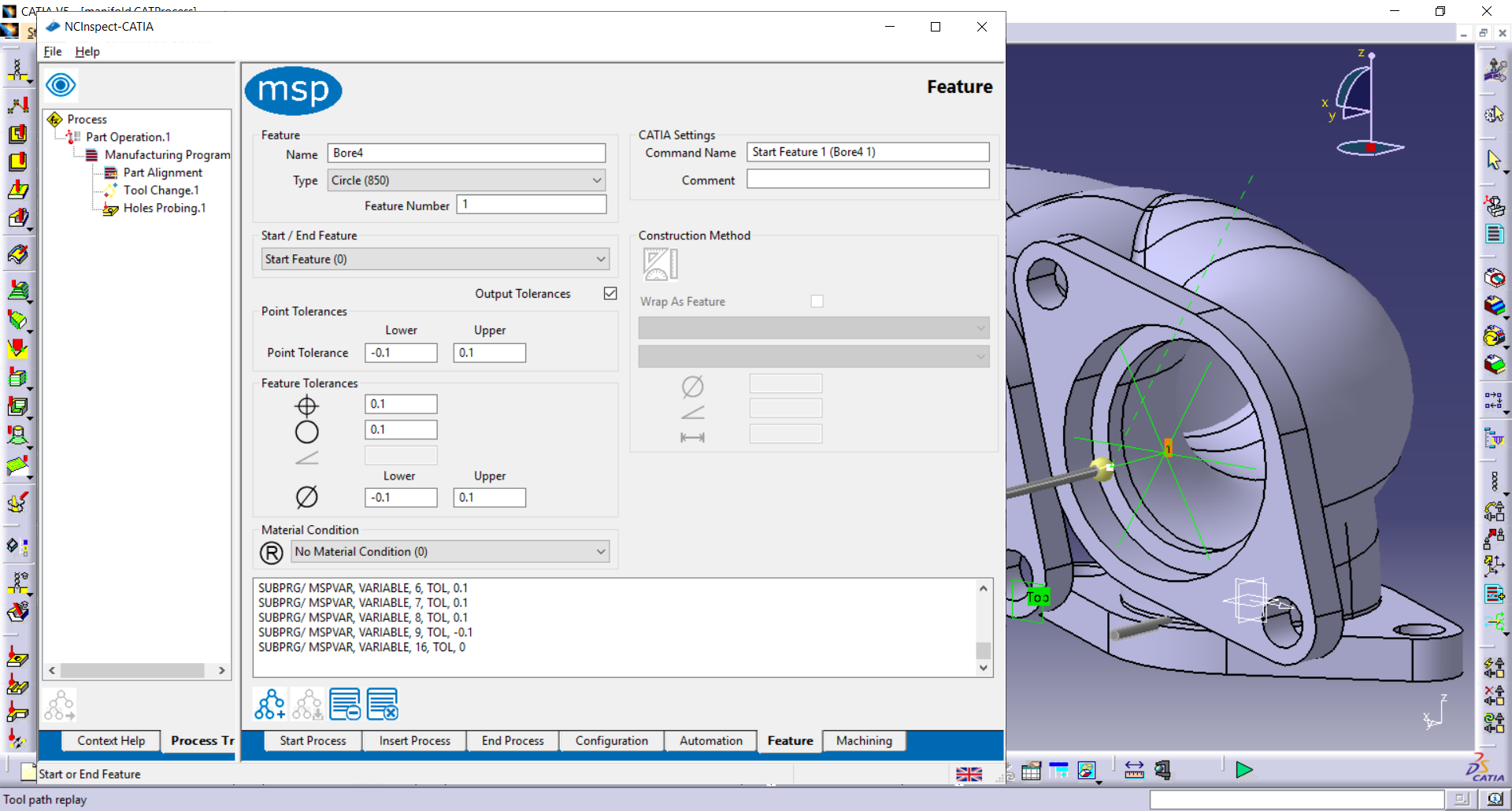
MSP's engineers have been helping customers with remote programming support.
Expert process analysis
MSP is regularly called upon to analyse each stage of a customer’s part process, from their CAD creation, probing routines through to their fixturing solutions. By applying their cross-industry experience, MSP can recommend new strategies to improve efficiency and, ultimately, part quality. MSP is continuing to support customers remotely in the UK and internationally - most recently collaborating with associate company, Renishaw, in Canada. MSP helped Renishaw understand their customer’s machining capabilities and advised how best to adapt the setup and alignment strategies to accurately produce a new family of components.
As MSP engineer, Stefan Hafner, describes:
“These parts are the most complex the company has ever machined and their current process would not meet the incredibly tight tolerances the end user had defined. We were able to liaise with the customer and Renishaw to support and install NC-PerfectPart which will now automate the majority of their manual processes and allow on-machine inspection. This will massively reduce the heavy burden on their quality teams. The results so far have been impressive and we will continue to support them and make further changes so they can evolve and improve as their inspection rate increases”.
Tailored technical workshops
MSP is currently hosting closed technical workshops for customers who are interested in understanding the new features that are being released in NC-PartLocator and its associated products, and how these will benefit customers on the shop floor. Within these sessions, customers are encouraged to share their current part production challenges and MSP shares advice on how to improve them by making use of all the features available in their products.
MSP intends to open up these workshops to manufacturers who don’t currently work with MSP so that they can also benefit from MSP’s expert knowledge. MSP is keen to share its knowledge of part production processes to support other organisations in the industry so the manufacturing sector can recover as quickly as possible once the pandemic restrictions are lifted.
If you are interested in arranging a workshop for your team, register your interest here.
Peter Hammond, MSP Technical Director, summarises:
“The impact of COVID-19 on the manufacturing industry has been huge and it will clearly take a long time to recover. In these new and uncertain times, we want to assure our customers that we continue to be here to support them in whichever way they need. I’m delighted we have been able to have such a positive impact on so many customers during this time. The industry will recover and MSP, and our customers, intend to be at the forefront - leading the way”.
Share this
- May 2025 (1)
- February 2025 (1)
- December 2024 (2)
- November 2024 (1)
- September 2024 (1)
- May 2024 (1)
- December 2023 (2)
- November 2023 (4)
- October 2023 (2)
- September 2023 (1)
- August 2023 (1)
- July 2023 (2)
- June 2023 (2)
- May 2023 (1)
- April 2023 (1)
- March 2023 (2)
- February 2023 (2)
- December 2022 (1)
- November 2022 (1)
- September 2022 (1)
- July 2022 (2)
- May 2022 (1)
- January 2022 (1)
- October 2021 (1)
- August 2021 (1)
- March 2021 (2)
- February 2021 (1)
- September 2020 (2)
- May 2020 (1)
- March 2020 (1)
- January 2020 (2)
- December 2019 (1)
- November 2019 (1)
- October 2019 (3)
- August 2019 (1)
- June 2019 (1)
- May 2019 (1)
- April 2019 (2)
- March 2019 (1)
- February 2019 (3)
- December 2018 (1)
- October 2018 (1)
- September 2018 (1)
- August 2018 (1)
- July 2018 (1)
- June 2018 (1)
- May 2018 (1)
- April 2018 (1)
- October 2017 (1)
- August 2017 (1)
- July 2016 (1)