Share this
Innovative manufacturing solutions halve set-up time for composite part production
by MSP Marketing on 9:23 AM on February 1, 2019
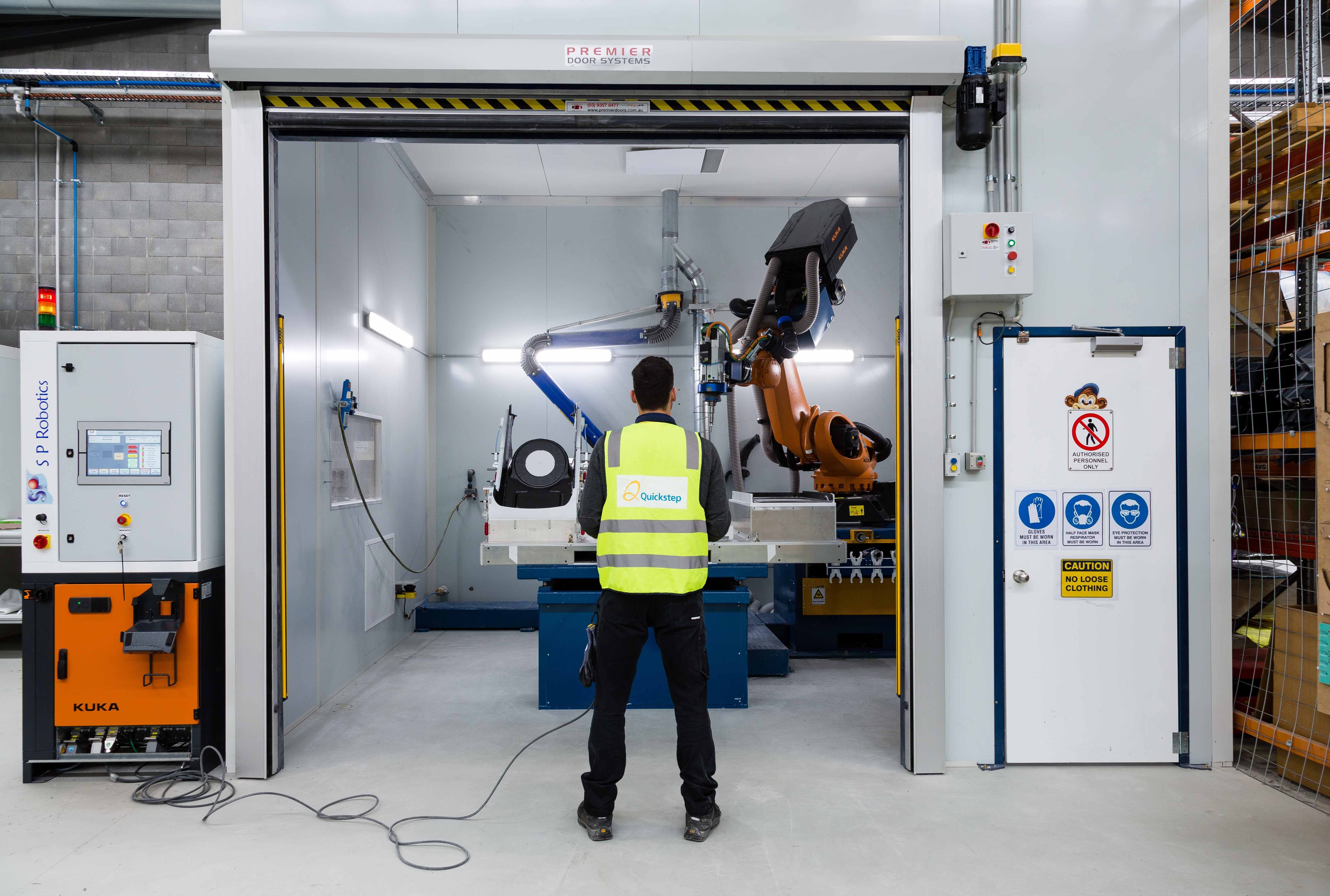
The combination of MSP’s NC-Checker and NC-PerfectPart software with Renishaw’s leading probing technology, is delivering significant cost and time savings for Quickstep Technologies’ composite manufacturing processes.
MSP, who are an associate company of Renishaw PLC, are global experts in developing and implementing precision metrology software, helping companies within various sectors, such as the Aerospace, Formula 1, and Defence industries, produce 100% accurate parts. Their innovative software makes manufacturing processes more efficient and helps customers, like Quickstep Technologies, reduce costs, scrap parts and manufacturing time significantly.
Quickstep Technologies is the largest independent aerospace grade advanced composites manufacturer in Australia, providing solutions to customers including Northrop Grumman, for who it is an approved supplier for the international F-35 Lightning II Joint Strike Fighter (JSF) program.
Challenge
Kris Dokka, Specialist Manager, Quickstep Technologies explains: “The JSF program requires the supply of high-precision composite manufacturing and involves a high degree of precision machining, specifically five-axis work for parts, and therefore consistency, qualification, documentation and traceability were pre-requisites for this contract. Confidence in the machining and quality process was also paramount and we had to be confident that the equipment and processes could deliver the job.”
Kris continues: “The parts we produce are complex free form shapes, so work-holding is a major issue when using traditional manufacturing methods. Each part has a dedicated composite vacuum fixture with three or four fixed location Tooling Spheres. The centre point of the spheres are known relative to the part geometry and this information is then used to locate the fixture or part in a suitable work offset coordinate system for machining. Prior to using NC-PerfectPart, these datums were generated using standard cycles within the Siemens control. While this achieved results, it was limited in that it was time consuming and open to human error.”
Solution
Implementation of MSP’s NC-PerfectPart and NC-Checker software, supported by the use of a Renishaw RMP600 radio probe, provides the detailed information required to monitor the accuracy and capability of Quickstep Technologies’ five-axis machining, ensuring their machines stay within specified parameters.
NC-Checker first carries out a calibration check on the probe. Once this is complete, it then proceeds to carry out five-axis checks of the machine tool to check the machine’s accuracy. This produces a benchmark report which shows the manufacturer if their machine is capable of machining parts to tolerance. The software provides detailed results in a comprehensive report and can show precisely where the machine may be under-performing. This check takes minutes to complete, meaning it can be run on a regular basis to provide routine monitoring of the machine’s geometry.
NC-PerfectPart fully automates the datum setting and verification process and therefore eliminates any human error. NC-PerfectPart also removes the need to precisely position the part, saving significant time in setup.
Results
Kris continues: “Automating our datum setting and verification process reduced our part set up time by 50% per part (when compared to the previous method).
Due to the simplicity of the software, we now have a scheduled fortnightly benchmark execution routine. Assessing the machine using our old methods could take anywhere between 2 and 4 days to complete. With NC-Checker, and the use of a Renishaw RMP600 radio probe, we have simplified the procedure greatly and can now complete this check in 1-2 hours, a saving of up to 96%, freeing up valuable machine time and improving productivity.
As the software is used prior to any machining, it provides us with assurance about our processes. We can understand if the machine is still capable of producing parts to the required geometric tolerances. Part analysis can be also conducted before any cutting, eliminating uncertainty and possible costly rework and/or scrap. Last year we achieved a 75% reduction in rework and this year are aiming for Gold.”
Without this ability to map the machine tool with NC-Checker and qualify the accurate position of the component in the machine with NC-PerfectPart, it is virtually impossible to guarantee a perfect part, without significant time and cost implications.
To read the full Quickstep case study, please follow this link.
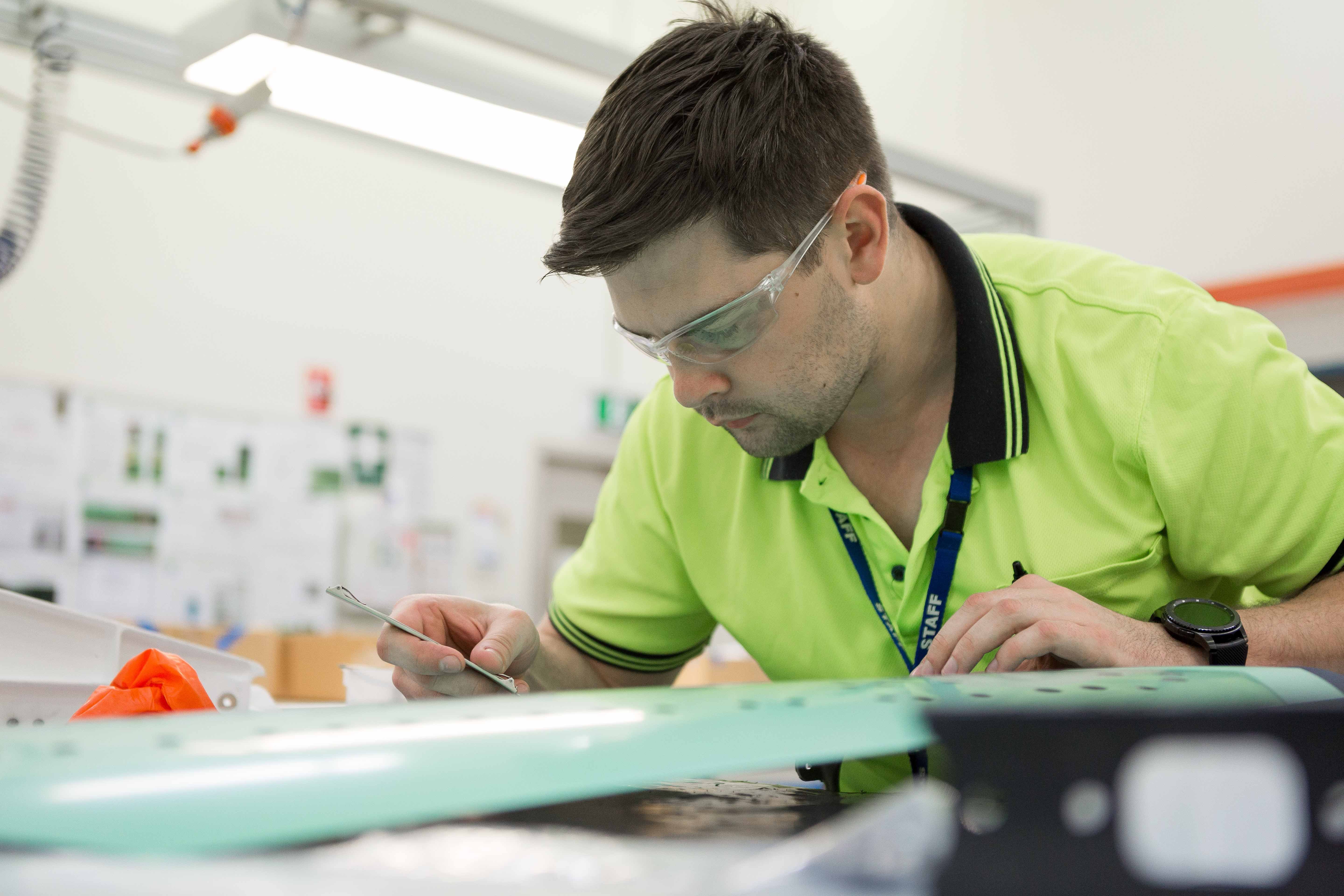
Share this
- May 2025 (1)
- February 2025 (1)
- December 2024 (2)
- November 2024 (1)
- September 2024 (1)
- May 2024 (1)
- December 2023 (2)
- November 2023 (4)
- October 2023 (2)
- September 2023 (1)
- August 2023 (1)
- July 2023 (2)
- June 2023 (2)
- May 2023 (1)
- April 2023 (1)
- March 2023 (2)
- February 2023 (2)
- December 2022 (1)
- November 2022 (1)
- September 2022 (1)
- July 2022 (2)
- May 2022 (1)
- January 2022 (1)
- October 2021 (1)
- August 2021 (1)
- March 2021 (2)
- February 2021 (1)
- September 2020 (2)
- May 2020 (1)
- March 2020 (1)
- January 2020 (2)
- December 2019 (1)
- November 2019 (1)
- October 2019 (3)
- August 2019 (1)
- June 2019 (1)
- May 2019 (1)
- April 2019 (2)
- March 2019 (1)
- February 2019 (3)
- December 2018 (1)
- October 2018 (1)
- September 2018 (1)
- August 2018 (1)
- July 2018 (1)
- June 2018 (1)
- May 2018 (1)
- April 2018 (1)
- October 2017 (1)
- August 2017 (1)
- July 2016 (1)