Share this
What is machine tool metrology?
by MSP Marketing on Apr 15, 2025 1:23:32 PM
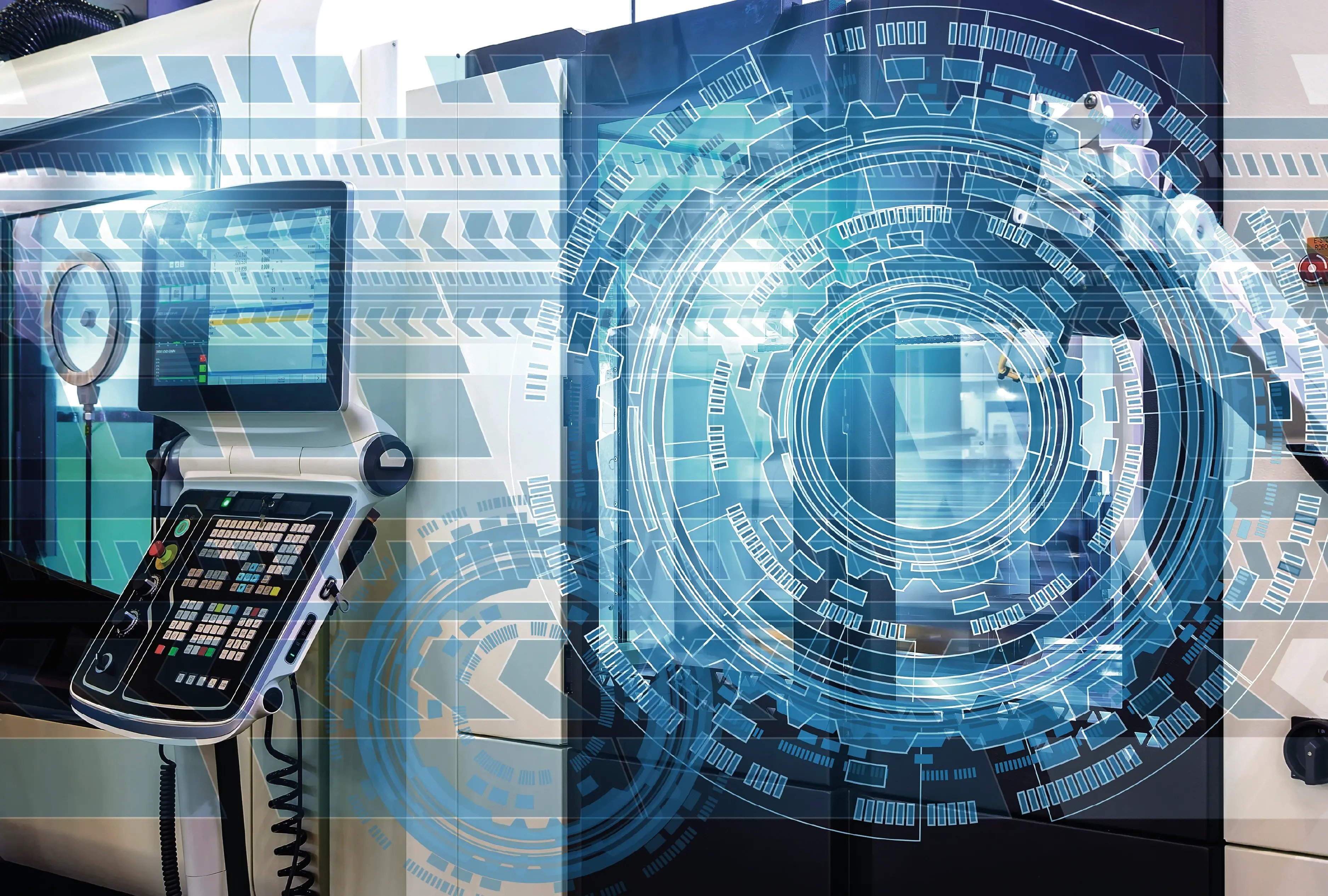
Defining machine tool metrology
In a general sense, metrology is the science of measurement and its application. More specific types of metrology include machine tool metrology which is concerned with measuring and maintaining the accuracy and performance of a machine tool or part machining metrology which is concerned with measuring the accuracy of the parts produced.
Metrology equipment to facilitate this measurement or maintenance includes dial test indicators, squares, length bar, spindle probes, lasers and automated CNC metrology software. The latter is the most accurate as it is the only type of metrology that can remove manual involvement from the measurement process.
When might this be useful?
If manufacturers are machining parts without the proper use of metrology to monitor or maintain their machine tool, they run the risk of inaccurately machining parts. If the machine is not setup correctly, if there are errors elsewhere on the machine or if it is unknown that the machine is underperforming, this is a recipe for scrapping parts or producing parts which need to be reworked or sold as concessions.
Accurate metrology systems are especially important for 5-axis CNC machining where machines tend to be more complex and parts have higher tolerance requirements. In this scenario, specialist metrology systems that monitor the machine tool’s performance and uncover hidden errors that would not be found any other way should be considered.
Furthermore, if the machine tool metrology is digital, this can feed into industry 4.0 data systems for increased knowledge sharing and connectivity across the entire shopfloor.
Overall, machine tool metrology can provide much needed confidence for manufacturers in trusting their machine tools, machining processes and the parts being produced.
Other benefits
If using automated metrology software for your machine tool, it can provide other important benefits. Examples of this automated metrology software for CNC machines include MSP’s NC-Checker. This product offers an automated metrology solution to assess the geometric performance of the CNC machine tool. It confirms if the machine is capable of producing a part to within tolerance and highlights any error on the machine tool so this can be removed before machining begins. Manual involvement is removed and the machine can be confirmed as ‘green to go’. Other benefits include:
- Machine downtime reduction: Machine assessments are performed automatically in 20 minutes, reducing the amount of time the machine is required to be sat idle.
- Predictive maintenance: This software monitors machine performance over time making it possible to predict when maintenance may be needed and avoid crashes or machine emergencies. It also allows maintenance to be scheduled in at an appropriate time for production.
- Part to part variation elimination: If manufacturers are struggling with varying part quality from a single machine tool or seemingly identical machine tools, NC-Checker’s metrology data can provide useful insights. Performance can be compared over time and between multiple machines and the data can be analysed to understand why the difference is happening. If all issues are reduced, then the variation between parts will be reduced too.
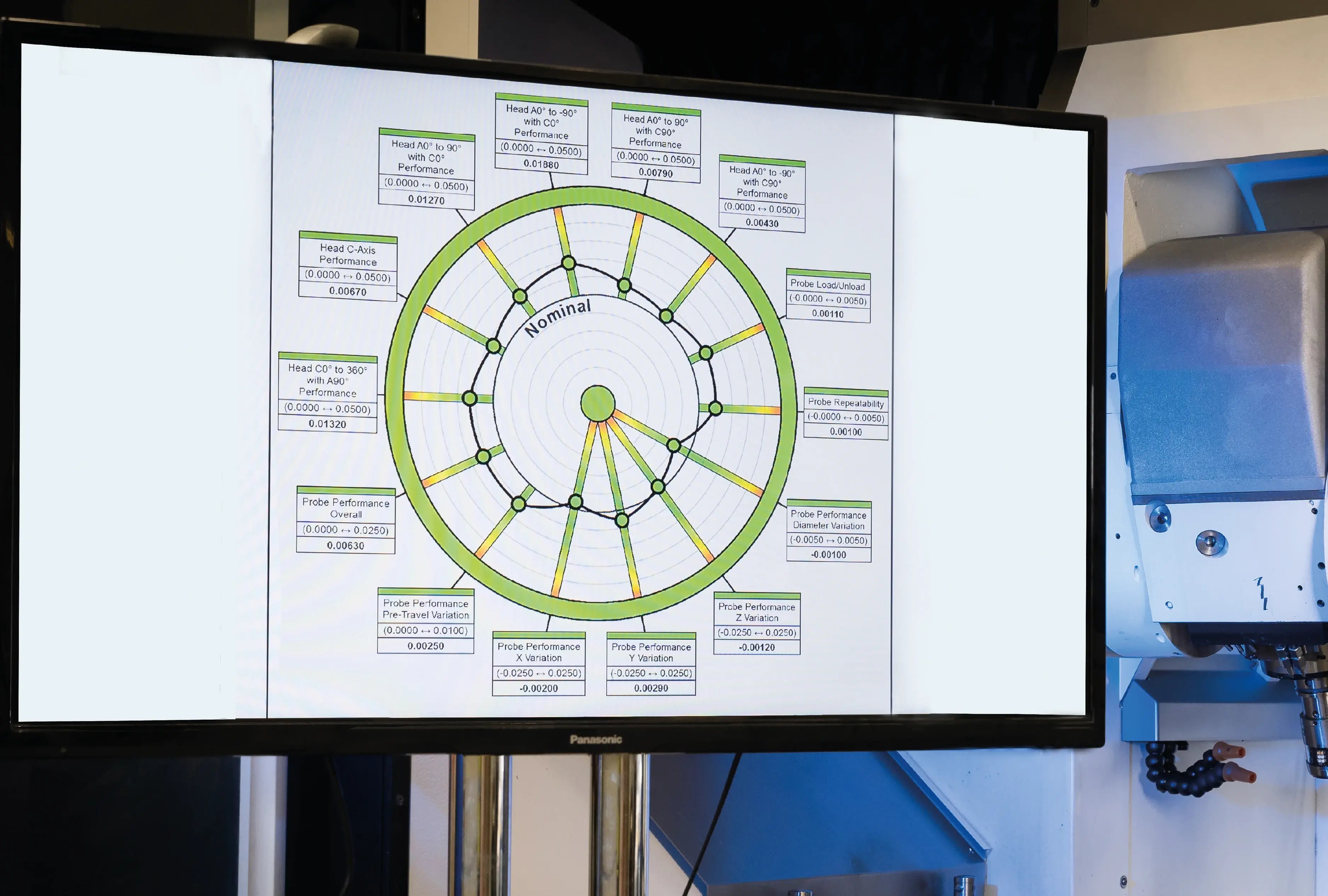
MSP's NC-Checker offers an automated metrology solution to assess the geometric performance of the CNC machine tool.
Things to consider
Metrology has important benefits for the machine tool, but it is also vital elsewhere in the CNC machining process. Just as metrology can highlight or remove errors with the machine tool, it can also remove errors in probe setup, probe calibration and part alignment processes.
Metrology devices, such as AutoClock from MSP, remove error from the probe setup process by automatically finding the micron-accurate location of the calibration artefact. It is important for extreme accuracy at this stage to ensure the probe is calibrated accurately and producing correct data. For the part alignment process, MSP’s NC-PartLocator metrology software, assesses a part’s condition of supply to confirm if it is good enough to machine. It then also measures the part to automatically generate a correct alignment based on where the part ‘really’ is on the machine tool. The software removes misalignment errors to prevent parts being machined incorrectly and potentially being scrapped.
Summary
Machine tool metrology plays an important role for measuring and maintaining the accuracy of a CNC machine tool and should be properly considered by manufacturers. The true potential of metrology is only full realised however when digital systems are used and integrated within probe setup and part alignment processes too.
Get in touch if you would like more information.
Share this
- August 2025 (1)
- June 2025 (2)
- April 2025 (1)
- March 2025 (2)
- January 2025 (1)
- November 2024 (1)
- April 2023 (2)
- December 2022 (2)
- July 2022 (1)
- May 2022 (4)
- November 2021 (1)
- October 2021 (1)
- September 2021 (2)
- January 2021 (1)
- December 2020 (1)
- December 2018 (1)
- August 2018 (1)
- August 2017 (1)