Share this
Solving The Biggest Challenges In The Aerospace Manufacturing Industry
by MSP Marketing on Oct 26, 2021 4:25:00 PM
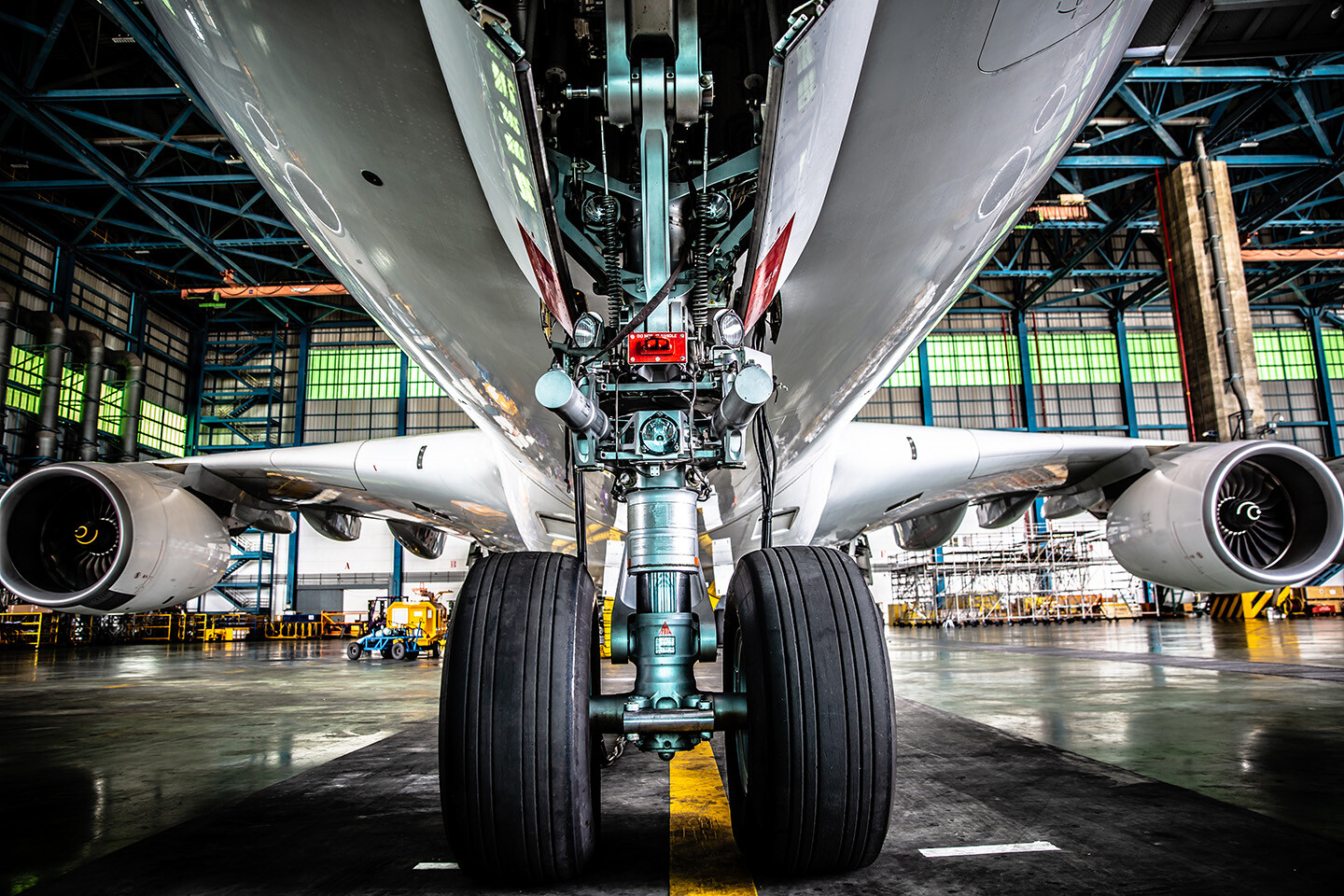
Do you work in aerospace part production and have a long list of problems you need to solve? Don’t worry, you are not alone.
In this article, we explore the most common challenges we’ve seen aerospace manufacturers face and, most importantly, how we help solve them.
How To Inspect Parts That Are Larger Than The CMM
In aerospace part manufacturing, parts are often too large to be measured with a traditional coordinate measuring machine (CMM). So what are your options? Before investing in a larger (and more expensive) CMM or other portable / laser CMM solutions, have you considered using your machine tool as a CMM instead?
We’ve helped many aerospace manufacturers do exactly this with the Post-Machining Verification feature in our NC-PartLocator software. The software measures the part on the machine tool bed after it’s been machined and confirms whether it is in tolerance or not.
This allows you to create an inspection process for large parts using your machine tool, eliminating the need to invest in new equipment. It also means reliance on the CMM is reduced and prevents parts being stuck in a bottleneck due to CMM backlogs. So it’s a win win!
What To Do When Normal Fixtures Aren’t Suitable For The Parts
Due to the complex, curved and varying nature of aerospace parts, a big challenge is aligning them correctly to tight tolerances without causing any distortion. And, if you didn’t guess already, we can solve this problem. In fact, we did exactly that for BAE Systems for the manufacture of skins for the F-35 program.
Before MSP got involved, BAE Systems would fixture their parts using vacuum, hydraulic or mechanical fixtures, but for their Nozzle Bay Door component, any of these fixtures would have distorted the configuration of the part. Instead, using NC-PartLocator’s ability to automate part setup, the BAE Systems engineering team developed an innovative part setup technique, known as sticky fixturing - a simplified way to hold a component in its free state while it is machined. Part setup was reduced from days to minutes and led to savings above £20million over the lifetime of the project.
How To Stop Part-To-Part Variation Across Machines
Your machines look identical. They appear to be working identically. So why are they producing parts of differing quality? The answer: there’s all sorts of things going on underneath the surface which might be affecting part quality that your machine isn’t alerting you to.
This is something we see a lot in aerospace product and part manufacturing that can be solved easily with NC-Checker. MSP’s NC-Checker software monitors a machine’s capability and highlights when the machine will not make a part to tolerance.
The results of the software can be compared across machines, and if there’s any difference in performance between the two, this will show up in visual Benchmark reports. NC-Checker helps identify what might be causing the problem, making it easier to fix the root of the variation between machines. This enables you to produce parts of uniform quality on different machines, and you can tick another problem off your list.
How To Confirm Part Quality To The Rest Of The Supply Chain
In the aerospace manufacturing industry supply chains tend to be complex and communication can be difficult, making it hard to prove part quality. At MSP, we have helped lots of companies combat this.
In the case of one of our Australian customers, Quickstep Technologies, consistency, qualification, documentation and traceability were all pre-requisites to becoming an approved supplier to the F-35 Lightning II Joint Striker Fighter (JSF) program. Confidence in the machining and quality process was paramount and both Quickstep Technologies and its customer had to be confident that their equipment and processes could deliver the job. Introducing our NC-Checker and NC-PartLocator software into their processes gave the customer the confidence they needed. The transparency of the reports and documentation that is automatically generated by MSP’s software gave them exactly the evidence they needed regarding ongoing machine health and accuracy.
If you work in aerospace part manufacturing and suffer from these problems, get in touch with us below to find out how we can help you solve them once and for all.
Share this
- August 2025 (1)
- June 2025 (2)
- April 2025 (1)
- March 2025 (2)
- January 2025 (1)
- November 2024 (1)
- April 2023 (2)
- December 2022 (2)
- July 2022 (1)
- May 2022 (4)
- November 2021 (1)
- October 2021 (1)
- September 2021 (2)
- January 2021 (1)
- December 2020 (1)
- December 2018 (1)
- August 2018 (1)
- August 2017 (1)