Share this
MSP Offers The Ultimate Fitness Tracker For Under Performing Machines
by MSP Marketing on May 4, 2022 4:32:00 PM
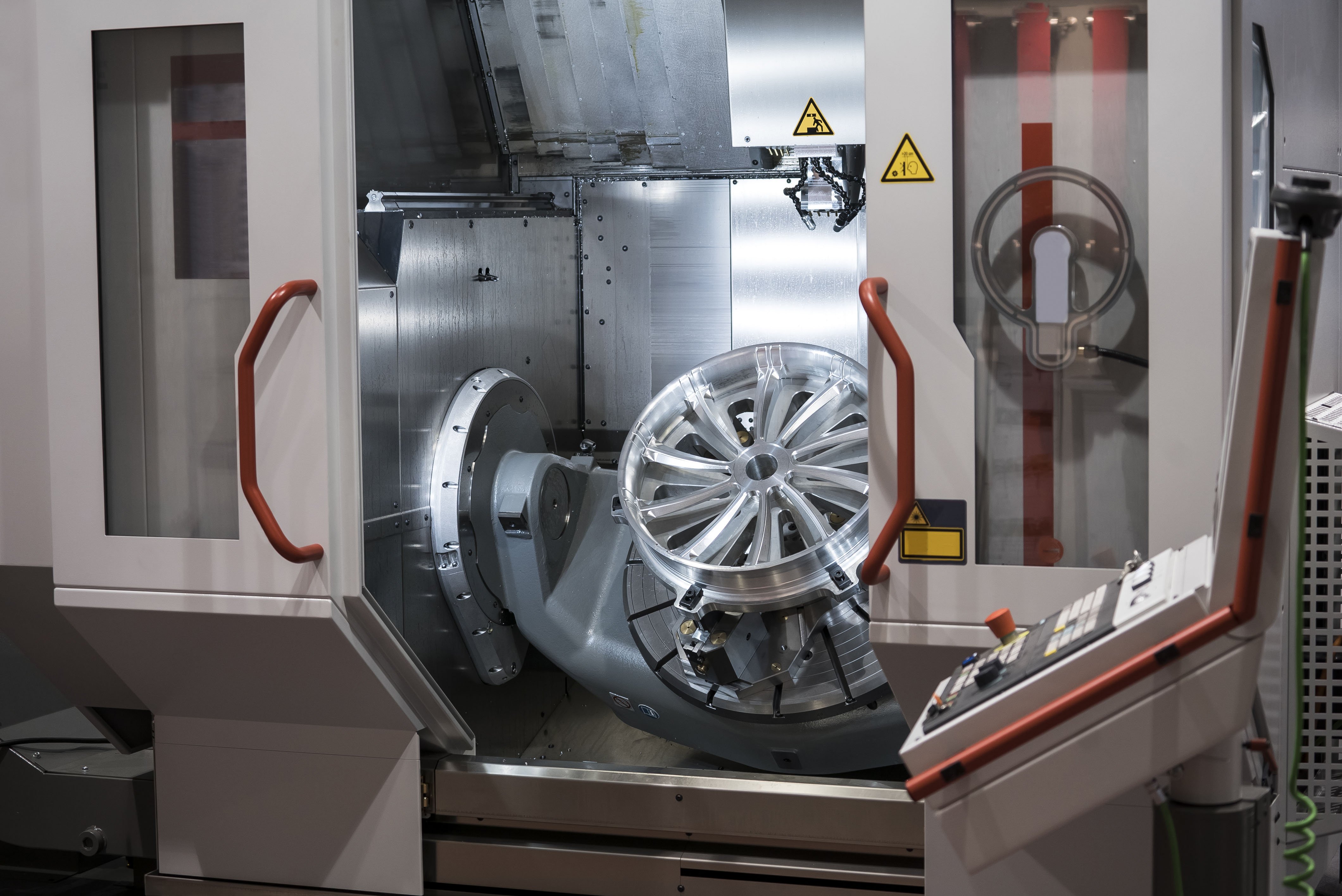
MSP has recently been making waves by helping manufacturers maintain their productivity and improve part quality, without having to make large capital investments in new machines.
The pandemic brought many challenges to the aerospace industry and companies had to find innovative ways to maintain productivity levels with fewer staff on site, without incurring additional costs. Frustrations also increased with costly maintenance visits that failed to improve part quality, especially when there was no budget to replace ‘faulty’ machines.
MSP’s products and support proved invaluable in solving these issues – enabling customers to analyse exactly why they were producing out-of-tolerance parts, and exactly how they could tweak their machine setup to maximise the use of existing equipment and resources.
Like a fitness tracker assesses the performance of an athlete, NC-Checker assesses the performance of a machine tool. It highlights if the machine is capable of producing parts to tolerance or if the machine is underperforming and, most importantly, how to fix it. Operators can react to NC-Checker’s reports themselves, or call for maintenance support armed with the information that explains precisely how the machine’s performance needs to be improved.
MSP Engineer Amanda Tait made a significant difference for one particular customer whose NC-Checker report showed that their rotary axis tests were displaying large kinematic errors. This indicated to Amanda that, while the mechanical performance of the axes were in good condition, the machine parameters relating to the kinematic point of rotation and pivot needed to be adjusted. These adjustments were capable of being made by the customer with expertise from Amanda during a 20-minute phone call, and their machine was back in production and making parts within 40 minutes. A maintenance call-out was not required and they saved £20,000 in fees and lost production.
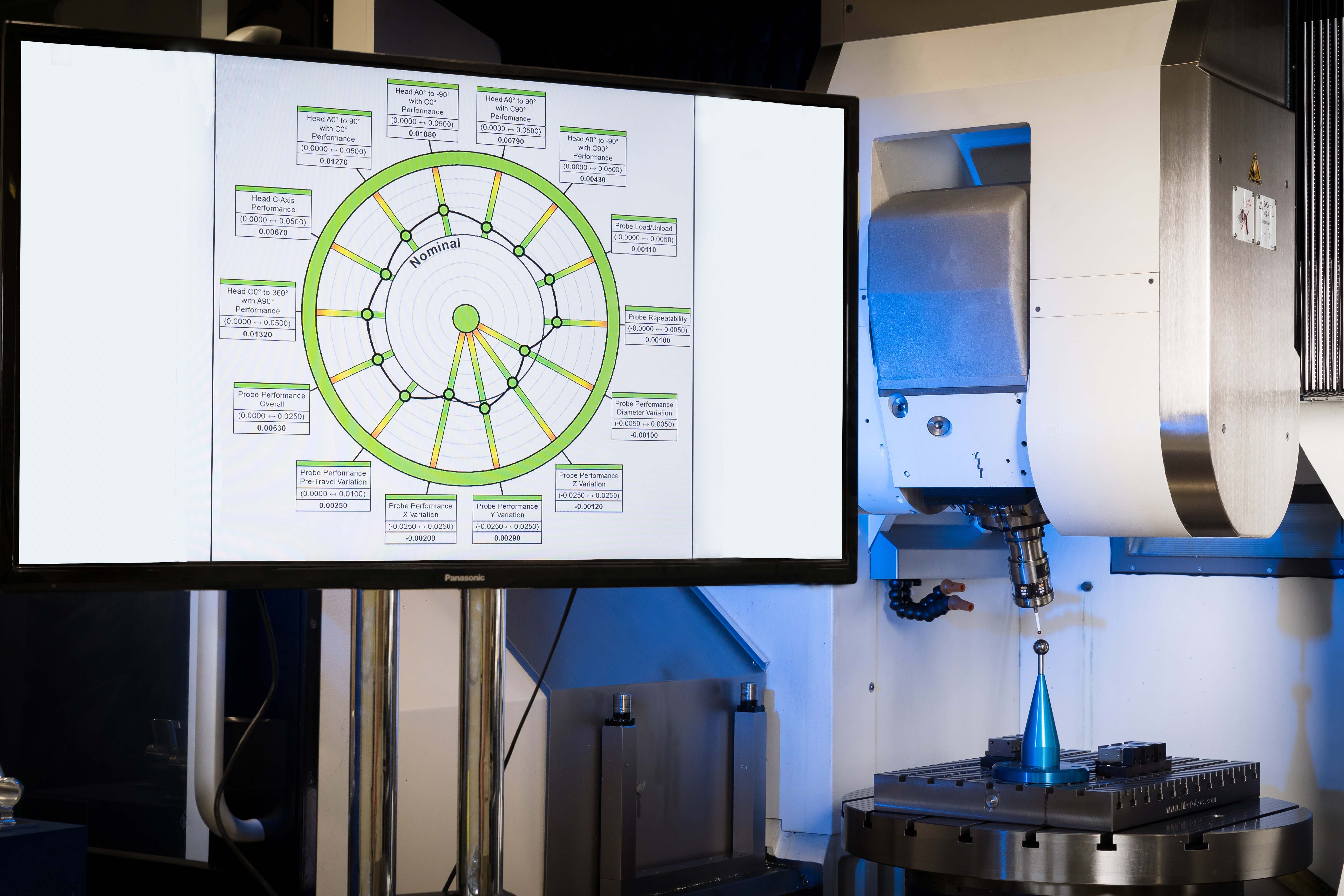
NC-Checker assesses the performance of a machine tool
NC-Checker uses probing to assess the machine’s geometric capability, and it is vital that the probe is calibrated accurately before running any NC-Checker tests to avoid such errors being interpreted as actual machine error. MSP’s AutoClock allows operators to automatically calibrate the sphere and set the machine’s work offset (Z) without having to use manual methods such as a slip gauge or Base Master. This automated set up eliminates human error from the probe calibration process – saving operator time, machine time and preventing any detrimental effects on part quality further down the line.
When performing its calibration routine, AutoClock mirrors the usage of the tool as it would be when cutting parts. This is in stark contrast to other tool pre-setters, like lasers, which do not account for any deviation when contact is made. This feature had significant benefits for one MSP customer when AutoClock revealed, and corrected for, a poor initial calibration setup that had been performed manually by the operator. The use of AutoClock to automatically calibrate the sphere guaranteed the improvements in part quality the customer was hoping for, but was missing out on due to their use of manual calibration techniques.
Since using AutoClock on their machines, several other MSP customers have gained valuable insight into why their machines aren’t achieving optimum part quality. Using AutoClock alongside NC-Checker, MSP has been able to further enhance their machine capability checks and maximise their understanding of why a machine is producing out-of-tolerance parts.
As MSP Director of Development, Marianne Whitfield, says: “Many companies mentally write off their older machines, yet those that invest in probing equipment that is accurately calibrated using AutoClock, with NC-Checker to understand their machines’ geometric performance, have greatly increased their machines’ lifespan and usefulness. I’m delighted we’re able to give customers, who initially thought they would have to replace their old machines, the confidence that those machines are still capable of producing perfect parts”.
To learn more about how we can help, please contact us.
Share this
- August 2025 (1)
- June 2025 (2)
- April 2025 (1)
- March 2025 (2)
- January 2025 (1)
- November 2024 (1)
- April 2023 (2)
- December 2022 (2)
- July 2022 (1)
- May 2022 (4)
- November 2021 (1)
- October 2021 (1)
- September 2021 (2)
- January 2021 (1)
- December 2020 (1)
- December 2018 (1)
- August 2018 (1)
- August 2017 (1)