Share this
How to align distorted composite parts in CNC manufacturing
by MSP Marketing on Mar 19, 2025 9:13:25 AM
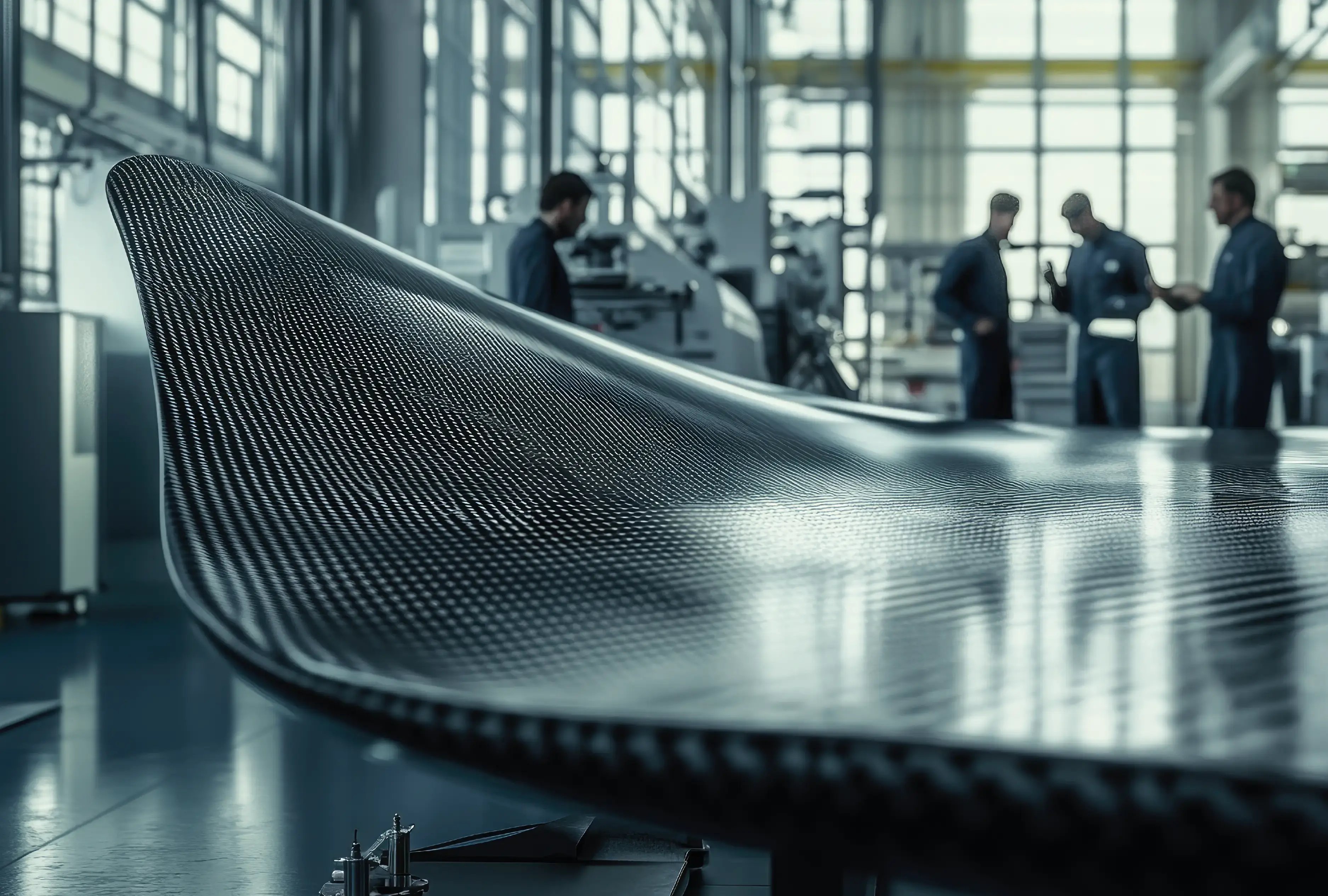
Composite material is widely used across the CNC manufacturing industry due to the material’s strong, yet lightweight nature, and its ability to mould into complex shapes. Composites like carbon fibre, Kevlar and glass fibre are prolific in industries such as the aerospace, automotive and marine sectors for parts including aeroplane wing structures, F1 aero parts and boat hulls.
Despite these positives, composite material has a dark side. It is prone to distortion which causes major issues for composite part manufacturing in terms of production and right-first-time pass rates. This article explores the reason behind this distortion and the solution to compensate for it in CNC manufacturing.
Distortion on composite parts
Composite material is sensitive to many processes that are involved in their manufacturing. Distortion and twist can occur during the curing and cooling process caused by non-uniform layup, creating problems from the outset.
These issues are detrimental to composite part manufacturing because it causes the part to differ from the CAD nominal. As this CAD data is used in traditional manual manufacturing methods to locate and hold the part on the machine, any discrepancies become an issue. Depending on how bad the distortion or errors are, parts may be machined incorrectly, holes may be drilled out of place or parts may have too much or too little material trimmed away. In most instances, this will result in the part being scrapped or needing manual rework.
What can be done about distortion?
Steps can be taken to minimise distortion on composite parts, however, due to the nature of the material, distortion will always be a probability. The answer lies in making the CNC manufacturing process adapt for the distortion instead.
CNC machine tool metrology can provide the solution. Automated metrology technology, like MSP’s NC-PartLocator, uses probing to automate part setup and detect distortion or errors on composite parts. The software generates the correct alignment of the part in the machine, accounting for the distortion, and automatically uploads this alignment to the controller.
Because the alignment will be correct for the part according to how much distortion / error is present (unlike hard fixture alignments based on the nominal CAD data) machining with this MSP alignment active will ensure the part will be machined to within the tolerances. Any errors due to misalignment are effectively eliminated from causing problems, saving parts from being scrapped or requiring rework.
As well as generating a global alignment for the whole part, the metrology software is also capable of creating local alignments for features common on composite parts and ones that are often difficult to machine to micron-accurate levels. For example, if you want to machine accurate counterbores or edge slots, the software can account for the surface distortion for these features and generate the correct alignment accordingly. This ensures the parts mate together correctly during assembly.
As well as generating alignments, the software is also capable of assessing the condition of supply for parts, a useful tool for composite part manufacturing. If the raw composite part is too distorted to clean up or align correctly, it can be assessed and rejected at the start of the process instead of spending time, money and effort machining the part, that will ultimately be wasted.
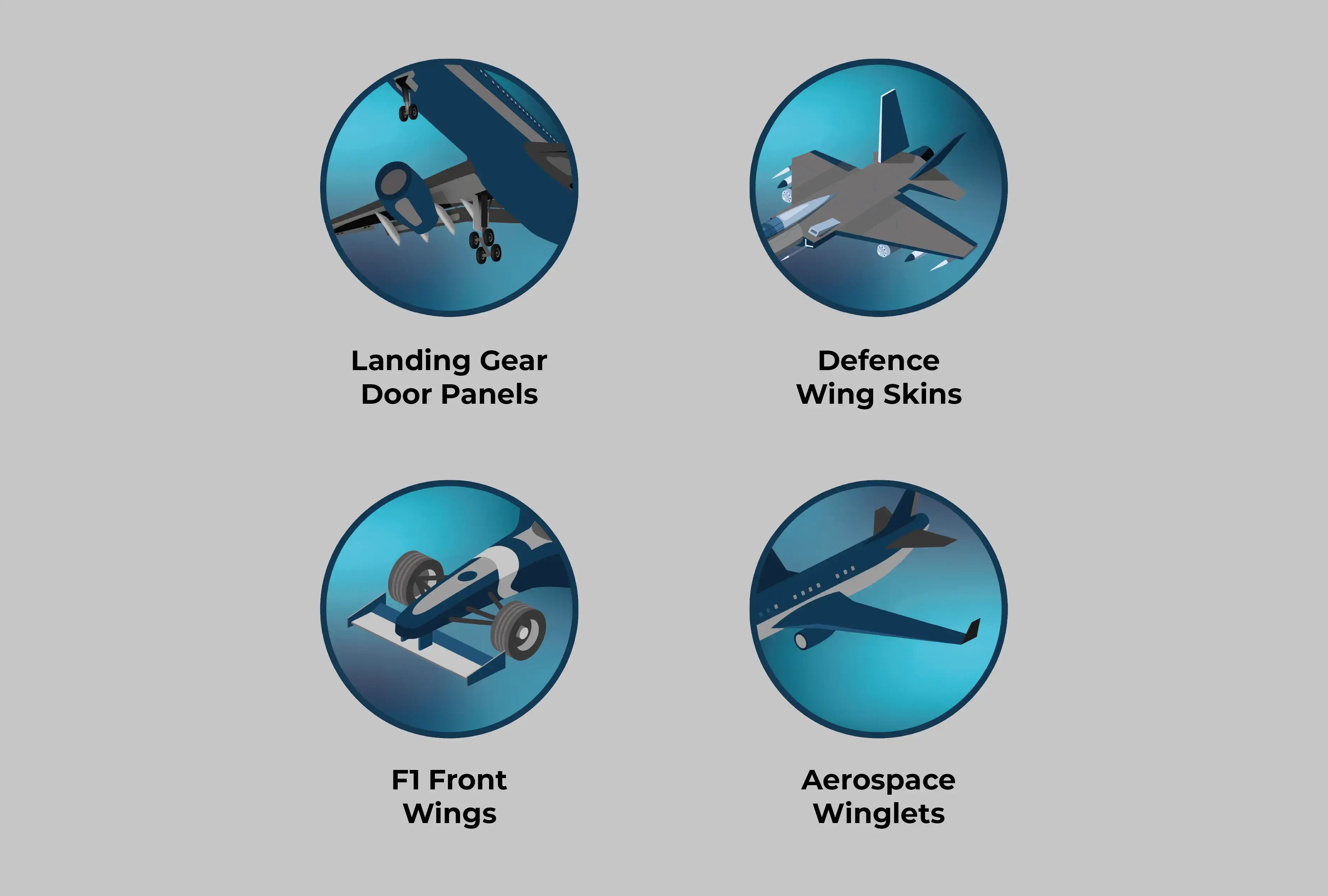
Composite manufacturers producing these sorts of parts have benefitted from automated part alignment solutions to compensate for problems like distortion.
Benefits
Creating micron-accurate part alignments for composites using machine tool metrology provides many benefits, including:
- Reduced part setup time: Alignments can be automatically generated in minutes, saving hours, or even days, trying to accurately position the part on the CNC machine tool.
- Better quality parts: Parts are finish machined right-first-time and pass final inspection.
- Repeatable processes: A stable and repeatable part setup routine is created, consisting of no manual operations.
- Easier fixturing: Simple fixtures can be used, eliminating the need to bend and constrain the part in the fixture to hold it correctly.
- Micron-accurate features and assembly points: Countersinks, counterbores and edge detail are machined to the correct depth.
- No scrap or rework: Scrap and rework are eliminated, saving valuable time, resources and cost.
Summary
Composites are versatile materials which have many applications in the aerospace, automotive and marine industries. The benefits of manufacturing parts from composites can be overshadowed by the material’s ability to bend, twist and distort during the various manufacturing processes it goes through before it is ready to machine.
This can be resolved using machine tool metrology solutions to account for distortion or errors on the composite parts. CNC software, like NC-PartLocator, uses probing to detect errors and generate an alignment that will compensate accordingly. The upload to the controller is automatic and the part can be ready to machine in minutes.
Finally, it’s possible to make the machining of composite parts as revolutionary as the material itself.
Share this
- August 2025 (1)
- June 2025 (2)
- April 2025 (1)
- March 2025 (2)
- January 2025 (1)
- November 2024 (1)
- April 2023 (2)
- December 2022 (2)
- July 2022 (1)
- May 2022 (4)
- November 2021 (1)
- October 2021 (1)
- September 2021 (2)
- January 2021 (1)
- December 2020 (1)
- December 2018 (1)
- August 2018 (1)
- August 2017 (1)