Share this
Adapting your manufacturing processes for ongoing restrictions | MSP
by MSP Marketing on Jan 6, 2021 4:13:00 PM
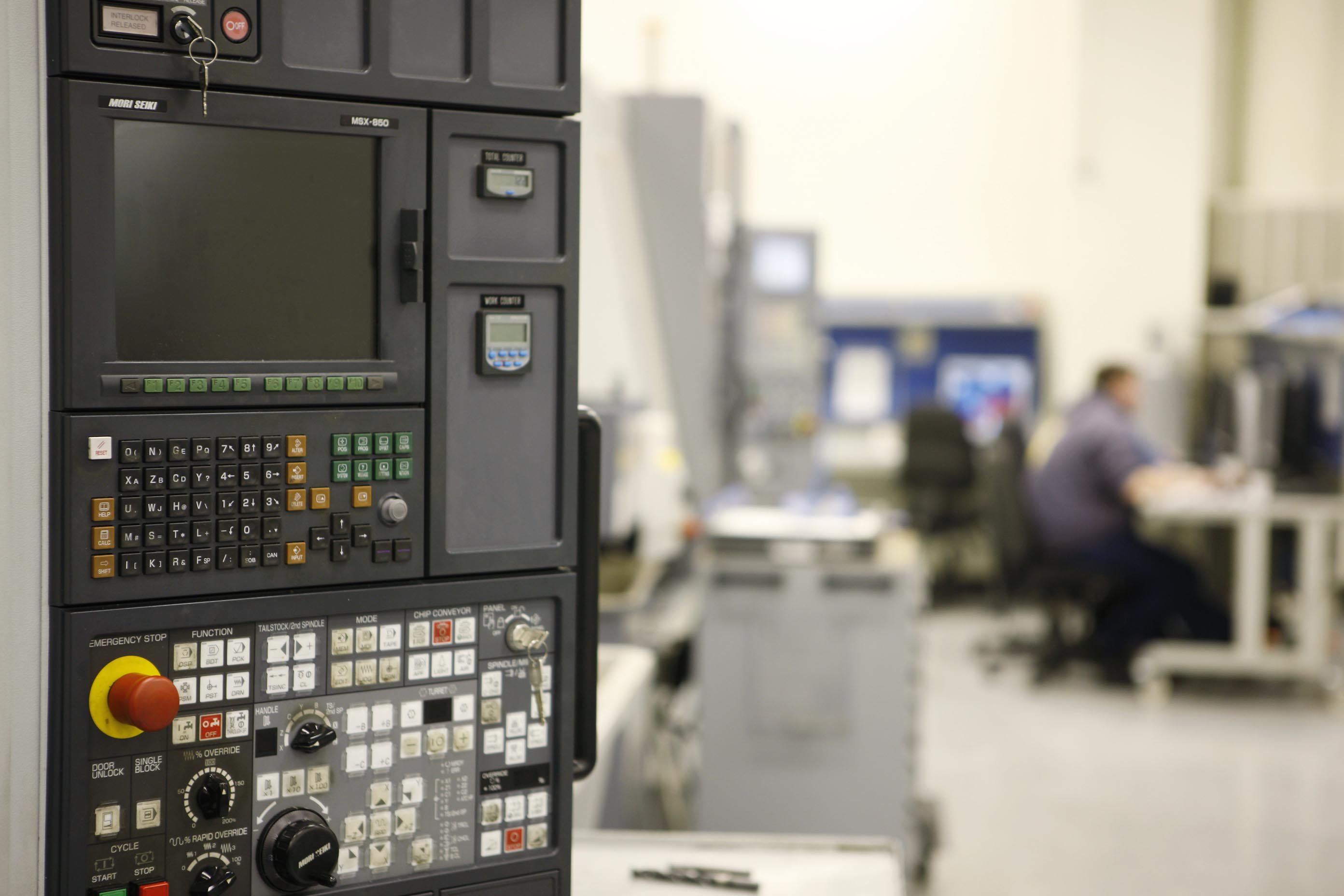
If 2020 taught us anything, working effectively and efficiently is more important than ever before. And with restrictions continuing into 2021, is it possible to keep productivity up, continue to win tenders and make profit?
The answer lies in the ability to be flexible and adapt machining processes accordingly. And while this might seem overwhelming to some manufacturers; it doesn’t have to be.
For key areas of the manufacturing process, simple changes can be implemented to overcome uncertainty over ever-changing restrictions and, more importantly, make processes sustainable for the long term.
Automation is the new normal
You’ve probably heard it before, but automation is a key starting point when looking to become more robust and adaptable.
Automating your production process ‘end to end’ will provide a stable process and produce quality components, same time every time. But most importantly, removing manual intervention from these processes means less personnel are needed on-site and can support the process remotely from the safety of their own homes.
And if this level of automation is alarming, be assured it doesn’t have to be. Companies like MSP make it simple to achieve a level of automation that will give you full confidence your parts will be made to tolerance when cycle start is pressed. Their suite of products are capable of running in full automation, offering 24/7 lights out operation; using the machine to its full capacity and giving operators the freedom to limit their contact on-site.
Optimise your production time
When restrictions are tight, you need to make every minute count. To start optimising production time, a vital first step is ensuring the basics like your calibration and machine tool are accurate and will operate within your required tolerances. Otherwise, you may waste valuable hours machining parts incorrectly and only find this out once you’ve received results from the quality team.
MSP’s NC-Checker is a good example of software which helps you understand what your machine is capable of. A simple report highlights where the machine is out of tolerance so the operator can pinpoint exactly what needs to be fixed. In an instant, they can see if the problem lies with the calibration, the probe itself or if it can be corrected with a kinematic fix. If its more serious and requires maintenance intervention, the maintenance team can use the same report to go straight to the issue - minimising their investigation time and the time your machine is out of production.
These simple reports can be tracked over time to plan preventative maintenance so you can take the machine down at a time that fits in with production, keeping schedules on track amid ongoing restrictions.
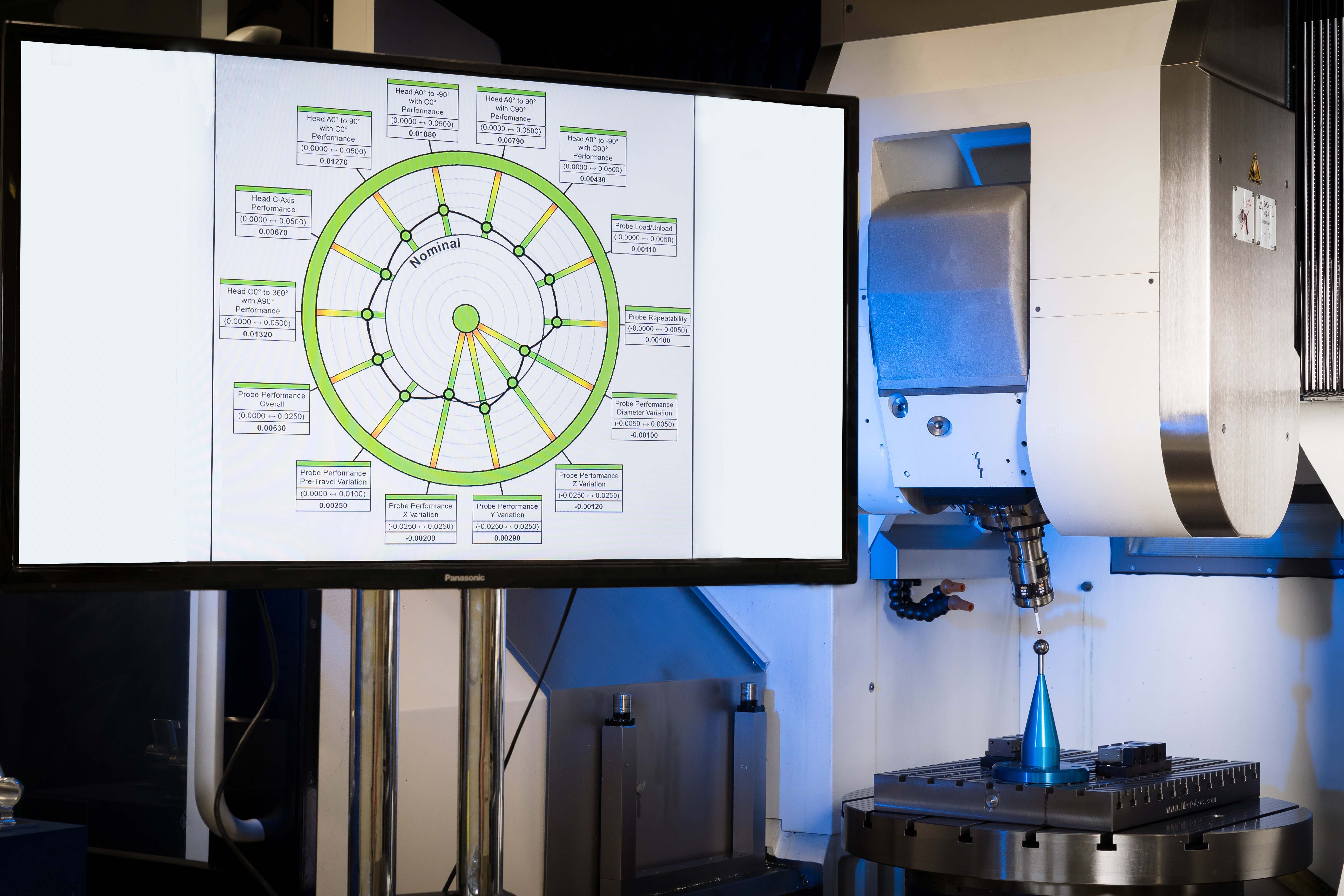
Manage machine performance and part production from anywhere
Managing your machines and part processes remotely during full production is key to successfully adapting to tightening restrictions and gives powerful flexibility to keep production on schedule.
Tools that allow you to manage the shop floor from anywhere, whether it be from your office, your home or even in a different country, are now a crucial investment for any manufacturing facility. MSP’s NC-Manager offers exactly this. Using this software, the user can observe the performance of all their machine tools and manage their parts from a single interface, away from the shop floor, minimising the amount of people on-site. A tangible game changer in times of uncertainty and ever-evolving guidelines restricting our movements and face to face interactions.
Diversifying into new markets
Change doesn’t get much bigger than moving into a new industry or market. But as work in key industries dries up, it seems inevitable for many manufacturers if they wish to survive. And whilst this may mean making big changes, there are ways of minimising this challenge.
In particular, removing manual part setup processes with automation gives a great amount of flexibility which can open the door to new industries.
Companies like MSP aim to make this transition from manual methods simple and have proven automation isn’t limited to a select few industries. Whether it be additive, composites, titanium or something more unusual, MSP’s automation solutions can be applied regardless. However complex the part or however challenging it may be to align, MSP’s solution will find the part where it really is and auto correct any misalignment at the press of a button. This helps design teams break free from the restrictions of what the production department are traditionally capable of machining and let their creativity and innovation take precedence.
Concerns over costly tooling and bespoke fixturing that come with entering a new industry can also be eradicated using this setup method. Automated setup means zero location fixtures and manual adjustments are no longer needed – all you need are simple fixtures which just ‘hold’ the part - meaning the same fixture can be used for multiple parts (within reason!).
With the right tools, anything is possible and worry over restrictions can be a thing of the past. And while restrictions will eventually ease, this new era of manufacturing is definitely here to stay.
Share this
- August 2025 (1)
- June 2025 (2)
- April 2025 (1)
- March 2025 (2)
- January 2025 (1)
- November 2024 (1)
- April 2023 (2)
- December 2022 (2)
- July 2022 (1)
- May 2022 (4)
- November 2021 (1)
- October 2021 (1)
- September 2021 (2)
- January 2021 (1)
- December 2020 (1)
- December 2018 (1)
- August 2018 (1)
- August 2017 (1)