Share this
The 5 Core Skills Needed To Improve Manufacturing Process Efficiency
by MSP Marketing on Sep 22, 2021 4:22:00 PM
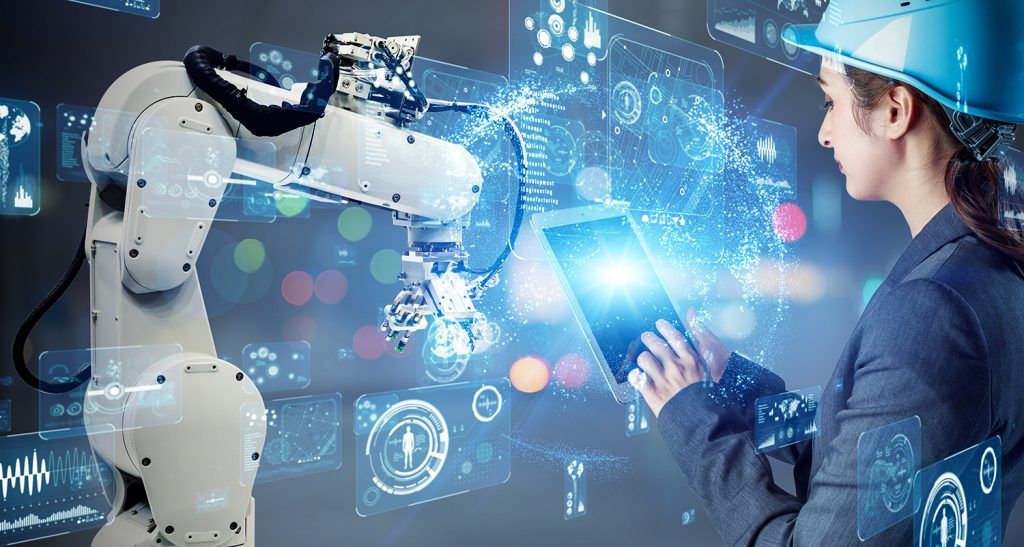
Automation is going to have a big impact on the efficiency of manufacturing processes over the next few years. Many people worry that automation is going to ‘steal’ jobs but, at MSP, we think the opposite is true.
Whilst mundane, manual and repetitive tasks can be replaced with high-tech equipment, computational power and robots, there are some human skills that will remain vital to improving manufacturing process efficiency.
Skill 1: Creativity
Creativity and the desire to push boundaries is a trait we have seen in many of our most advanced customers, especially in motorsport and composites. They are constantly looking for solutions that maximise the accuracy of their parts and reduce errors.
As processes become more refined, engineers and production managers need to be more and more creative with their ideas. Squeezing value and return on investment out of every stage of the manufacturing process has also become the norm, and even the smallest tweaks can have a major impact on cost-saving and efficiency.
Skill 2: Curiosity
We talk regularly to customers who are curious about how they can get more out of what they already have – including machine tools, fixturing, tool setters, and probes. There are some impressive tools out in the marketplace, but sometimes that new piece of kit doesn’t quite live up to the hype. The most curious engineers will try to ‘think outside the box’ and find out how they can make the equipment work to the best of its ability for their specific parts and processes.
Skill 3: Critical Thinking
Regular inspections and audits of production processes require the application of critical thinking. How effective is the current workflow? Where are the errors really occurring in the process? How can those errors be eliminated?
Automation can help to streamline workflows and business processes but it’s the critical thinking about where and how automation is best applied that will achieve the best results. MSP’s starting point when helping customers implement automation solutions is to find where human error is occurring in a process, and then eliminate it.
Skill 4: Collaboration
Manufacturing processes aren’t all about the machining – they involve collaboration with teams across the business, from part design through to manufacture and then inspection. It’s important that those teams understand how to get the best out of each other, and where they can help to create efficiencies across teams. Improvements in the functionality of CAD software and factory managements systems are all aiding collaboration and helping the most innovative companies to thrive.
And collaboration doesn’t just need to be internal. Some of the best examples of collaborative projects are those that involve suppliers as partners. Third parties often have the expertise and outward-looking perspective to drive improvements forward using their own equipment or software that internal teams may not have knowledge of.
Skill 5: Communication
People are still the most valuable asset in manufacturing and should be well trained and supported in their roles. Communication is key to getting the best out of people – and is even more crucial if staff are working from home, or are in different parts of the world, rather than present on the shop floor.
Sharing information about part processes has become a lot easier, but it’s important that the right information is shared at the right time. Industry 4.0 and ‘big data’ are facilitating huge amounts of data to be collected, and MSP works with its customers to make sure this data is used in the best way possible to keep them informed about the part process issues that really matter.
For more information about how we apply automation to increase our customers' productivity and efficiency and improve their teams' core skills, use the button below to get in touch.
Share this
- August 2025 (1)
- June 2025 (2)
- April 2025 (1)
- March 2025 (2)
- January 2025 (1)
- November 2024 (1)
- April 2023 (2)
- December 2022 (2)
- July 2022 (1)
- May 2022 (4)
- November 2021 (1)
- October 2021 (1)
- September 2021 (2)
- January 2021 (1)
- December 2020 (1)
- December 2018 (1)
- August 2018 (1)
- August 2017 (1)