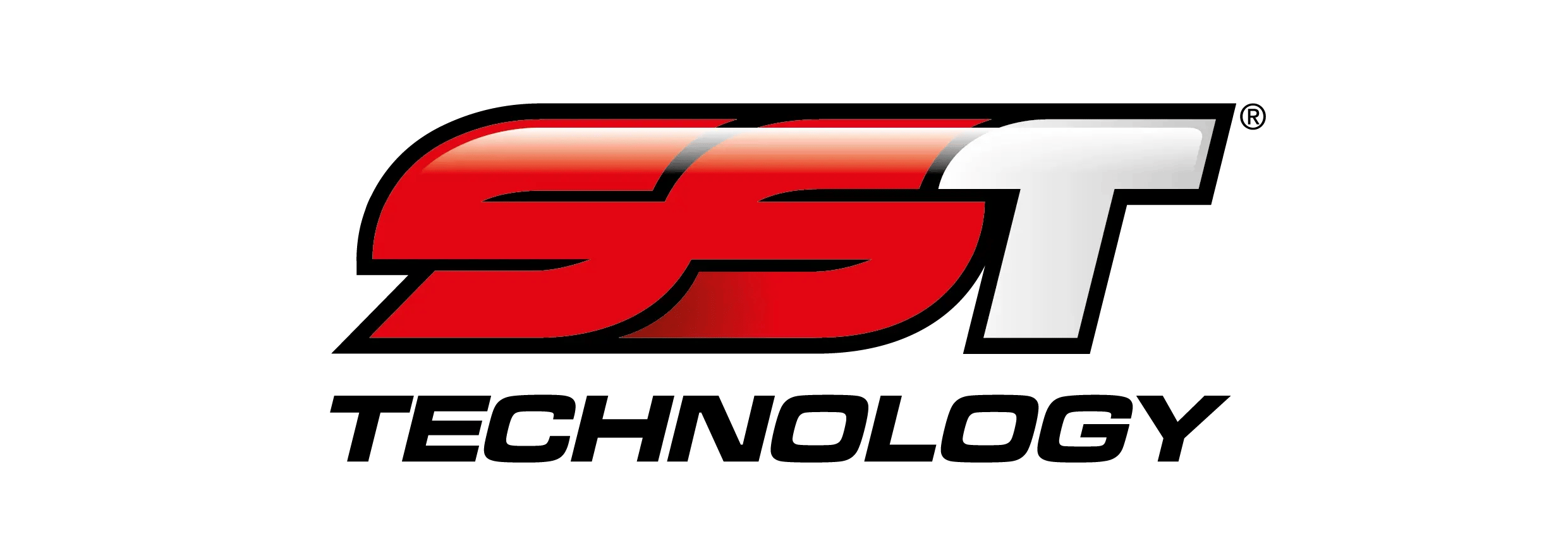
Engineering business producing 700% more parts with MSP's products
At a glance
A UK-based engineering business is now manufacturing up to 7 times more parts a week and has seen its part setup time reduced from 4 hours to 25 minutes, with the implementation of advanced manufacturing solutions from MSP to its additive manufacturing process.
Productivity Increase
MSP's solutions have enabled the company to increase their part production by 7 times.
Part Setup Time
MSP automated SST's manual setup process and reduced the time it took from 4 hours to 25 minutes.
Machining Cycle
Previously SST's machining cycle was 15 hours. Following the introduction of MSP, this was halved to 7.5 hours.
Products used
Background
SST Technology (SST), part of Polar Technology Group, specialises in the design and manufacture of engineered precision fabrications and thermal management systems for high-tech industries. SST’s experienced team partner with customers to provide a complete design, development and manufacture service.
“We strive to act as a technical partner to our customers rather than just a supplier, and aim to engage and understand our customer’s problems, to deliver solutions in excess of their original expectations,” explains Nick Henry, Technical Director at SST.
SST contacted MSP for their expertise to assist with a high performance Hypercar project, where they were experiencing non-conformance issues during the manufacture of Inconel 625 Additive Manufactured (AM) components for exhaust systems.
Due to the inherent challenges of additive manufacturing, these components have some dimensional variation from part to part. Subsequently, once the parts have been printed, final machining operations must take place on SST’s in-house 5-axis CNC machines to ensure they meet the extremely tight tolerances.
SST’s main aim for this project was to produce right-first-time parts and increase their productivity. To do this and successfully machine the parts, there were two key challenges they needed to overcome.
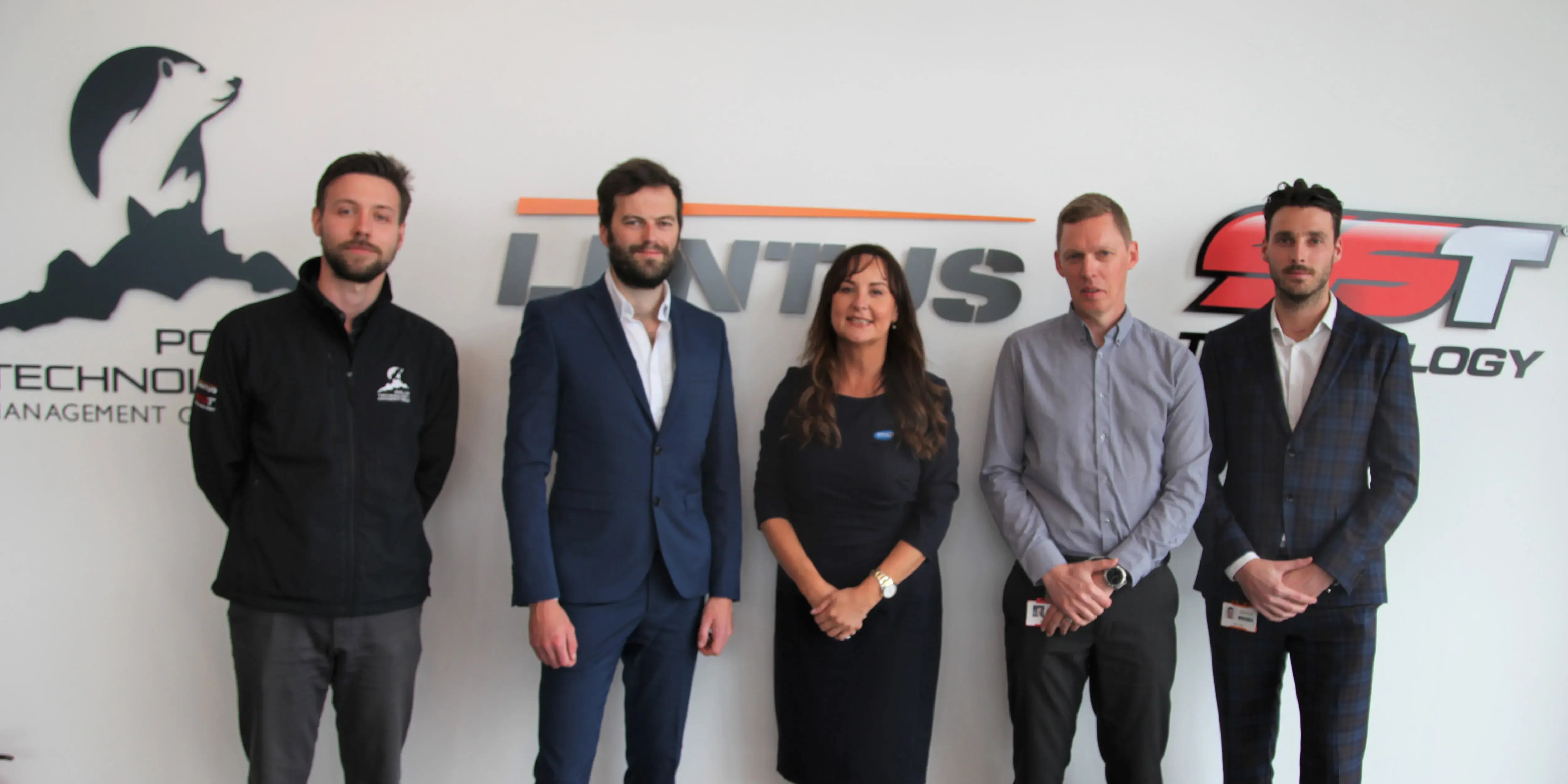
Challenge
The first challenge was the nature of the part itself; it is a 3D printed part with complex geometry, with a number of features existing in multiple orientations which made it difficult to achieve accurate alignments. As well as this, additive manufacturing is not a stable process and the parts it produces are not 100% accurate to the CAD model it originated from. Distortion can occur within the build process and finish machining on a CNC machine is often needed to bring the part into tolerance and ensure surfaces are smooth and flat as desired. This is difficult however, as a precise alignment is needed to cut the part accurately, something which is hard to achieve when it is unknown how the part has changed in the build process. In addition to this, fixturing difficulty, very little stock material and inconsistent condition of supply can also cause major frustrations.
Before MSP’s products were introduced, a highly skilled operator would manually locate the part in the fixture to ensure the alignment was accurate before machining. This involved multiple steps and was extremely time consuming to achieve the necessary accuracy. This, coupled with the human error caused by the manual elements, resulted in a vast amount of machine downtime and scrapped parts.
The second challenge was more of a general CNC machining challenge, SST needed to utilize the 5-axis functionality of their machine to ensure that it was operating to a high standard across all the axes in conjunction. There was no simple way to test or adjust this, as it involved using complex machine kinematics and the use of advanced measuring tools before machining took place, increasing machine downtime even further.
“Machine downtime was on average 5-6 hours a day before MSP”, said Thomas Clanfield, Quality Manager at SST.
“100% of my time was being used to fix issues on this project and it required an incredible amount of time from other senior level people in the business to resolve other problems, it was all hands on deck.”
Because it was such a time-consuming task to create a quality part, SST were having to find a balance between speed and quality. Their choice was to either invest more time in the manual part setup, and risk the detrimental effect on productivity, or just run with a poor setup to keep up with production, but risk the high chance of scrapping a part.
“This wasn’t sustainable for the business and we knew we needed to change things to maximise the productivity of our machines,” added Thomas.
Solution
To solve SST’s first challenge, MSP’s NC-PartLocator, from the MSP PerfectPart product suite, was installed on the CNC machine to automate part setup by calculating precise alignments for each machining operation. This removed the need for manual alignment, originally performed by a highly-skilled operator.
The software uses a 3D model of the part, in conjunction with 5-axis probing of the physical part, to derive an orientation which allows SST to establish the quality of the AM part and then successfully performs the finish machining. In addition to this, at every step of the process, the user is presented with graphical and textual information regarding measured results and how they compare to the 3D model. Any deviation in the AM print is also accounted for, and the feedback from the software allows users to understand more about major problem areas, any adjustments needed and also how to achieve repeatable print.
Previously, machining had to take place in multiple steps, with numerous CMM inspection points between each step, resulting in a lengthy process and reduced accuracy due to taking the part on and off the CNC machine. The introduction of NC-PartLocator meant that the probing of the printed component and the alignment of the CNC program could be performed in one operation.
“Before MSP, we were losing more parts than we were creating good parts and we couldn’t manufacture in one operation. We had to put the part on the machine, probe it, do rough cuts, measure it, put it back on the machine, re-cut it. With the introduction of MSP, not only can we remove all of these manual steps, but we can now check everything before cutting the part and resolve any problems that previously resulted in scrap parts.”
Brad Airey, SST Operations Manager
The second challenge was resolved using MSP’s NC-Checker. NC-Checker ensures the machine tool’s geometric performance is accurate enough for the part to be machined correctly. It produces automatic ‘benchmark’ reports for users to understand the performance and accuracy of the machine tool, before any machining begins. This is very important when working with AM parts that have little stock material.
“Using NC-Checker combined with a provided calibration sphere and the existing machine probe, we were able to get highly detailed info about our machine and probe about all manner of vital functions such as probe performance, repeatability and machine kinematic performance. This has allowed us to always be one step ahead, as we can go to our maintenance team and show them the benchmark with the machine issue diagnosed before they even have to look at the machine. This shortened investigation process means their time can be focused on fixing the problem,” said Thomas.
“NC-Checker gives us the confidence to trust that our machine will always make a good part. This enables us to focus solely on the machining of the part, without having to worry about issues related to the machine itself. And this benefit is not just specific to this job, it also extends to all our future machining work and projects at SST,” added Brad.
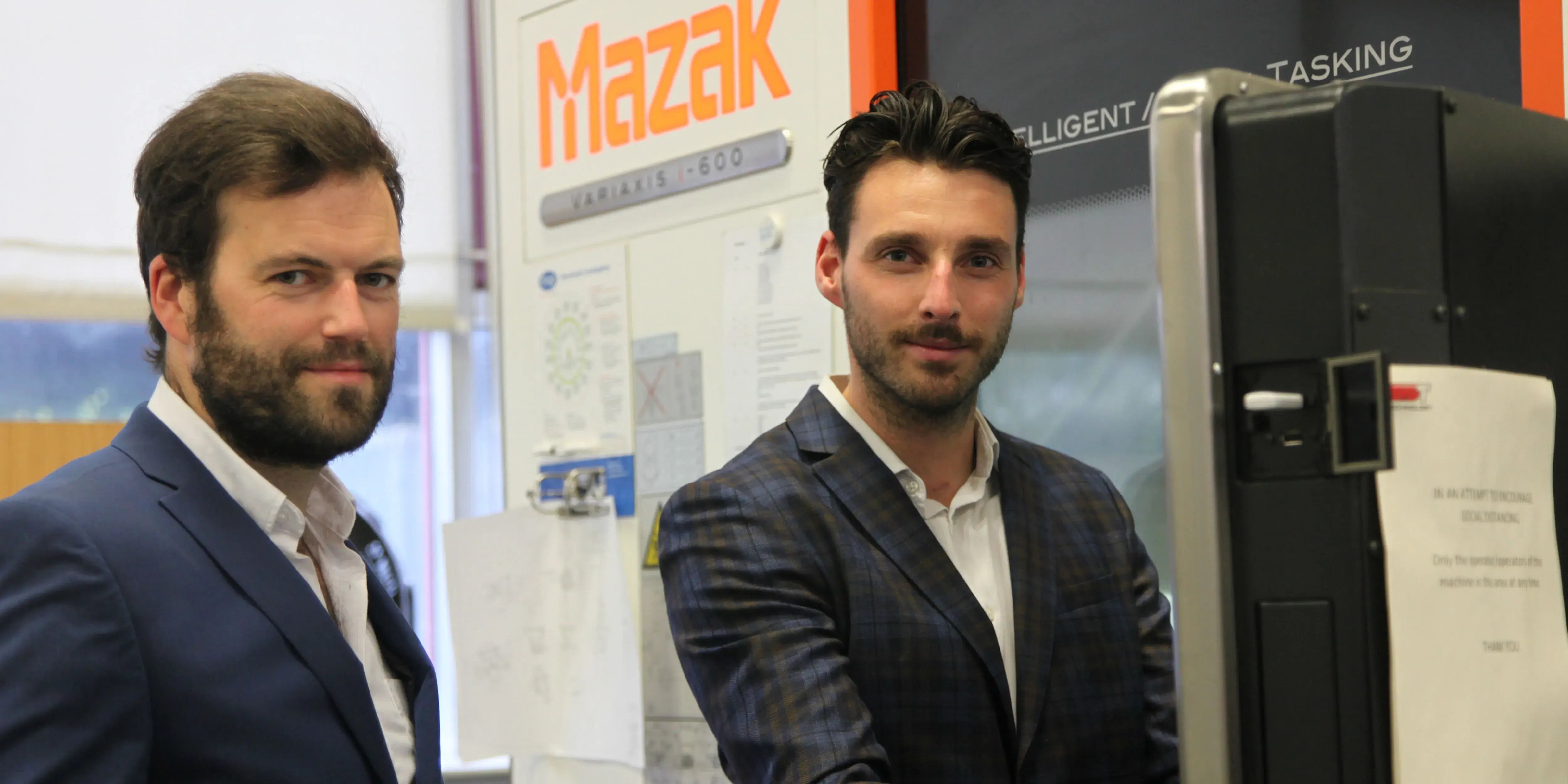
Result
By automating the manual elements in setup, MSP’s products reduced SST’s part setup from 4 hours to 25 minutes and, overall, halved SST’s machining cycle time from 15 hours to 7.5 hours. This has enabled the company to increase their part production by 7 times.
The elimination of inaccurate part setup and any machine issues also means the amount of scrap parts has also greatly decreased.
“This time saving has freed up the machine to create more parts and also produce parts for other projects. Because we also now don’t have to re-do parts that previously would have been scrapped, we can use the machine to make other parts that we would have previously had to sub-contract - as we just didn’t have the capacity before,” explains Nick.
Automation has transformed SST’s machine and part setup into such a simple process, that operators with no experience of the project are, with minimal training, able to run the machine 24 hours a day, with every shift, and alongside multiple other machines.
Brad said, “Beforehand, we would need highly skilled machinists to plot to the part manually and manually check that all the datums were setup correctly. We were struggling to find people of a high skill level to do this. Now we are able to run the machine shop with a reduced level of skill thanks to MSP’s solutions, confident that our parts will be perfect. This is possibly the greatest benefit of MSP’s solution and where it has had the biggest impact.
"We have also freed up the time of our highly skilled machinists so they are able to focus on other projects, to add value and improve processes elsewhere.
“Integrating MSP into the final machining process of our additive manufactured components has transformed the reliability and consistency of this process. It has allowed us to accommodate the inherent variables of additive manufactured components, whilst also retaining the tight tolerances of the finished part.
"It has also given us confidence to embark on new projects with new, similarly challenging parts, safe in the knowledge the MSP will help us achieve our goals".
Improving processes is an ongoing strategy for SST who are continually looking to improve the efficiency of their machine shop, increase production and reduce the strain on inspection and quality by implementing advanced manufacturing techniques, like MSPs, throughout the business.
After experiencing the benefits of adding these techniques to their additive manufacturing process, SST are now in discussions to implement MSP into their composite machining processes – an industry that MSP products have also achieved much success.
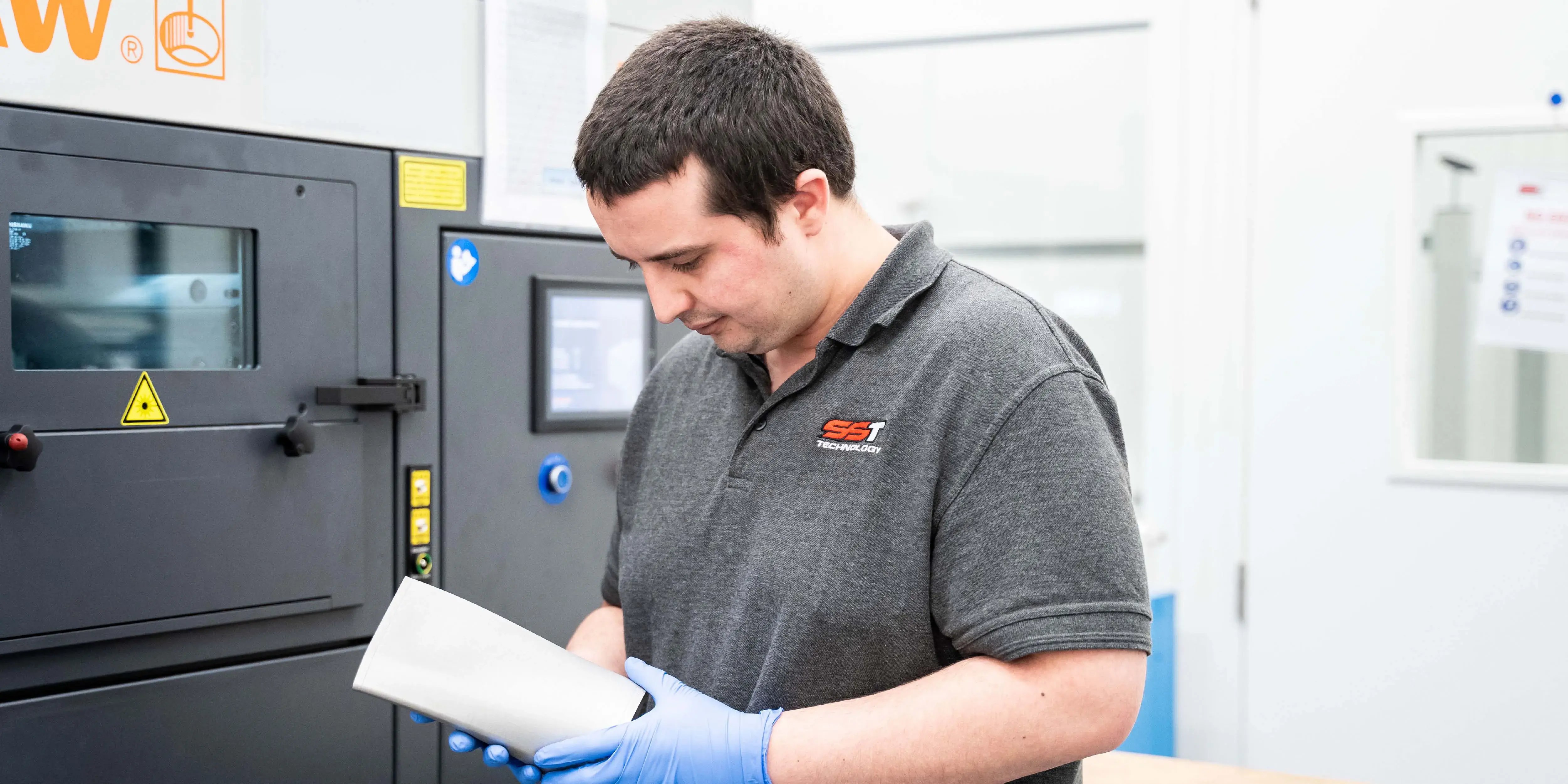
Be in a case study.
If you’ve had impressive results and want to be involved in your own case study, we want to hear from you! It’s a great way to shout about the collaboration between our great companies.